14
0
0
How to Maintain the Stability of a Steel Building Factory
10
zhengzhou
0
Maintaining the stability of a steel building factory is pivotal to ensuring the safety, efficiency, and longevity of the structure. Steel buildings are widely used in industrial applications due to their durability, strength, and flexibility. However, like any other construction, they require regular maintenance and attention to preserve their structural integrity. This passage explores various strategies and best practices to maintain the stability of a steel building factory, focusing on inspection, maintenance, environmental considerations, and structural enhancements.
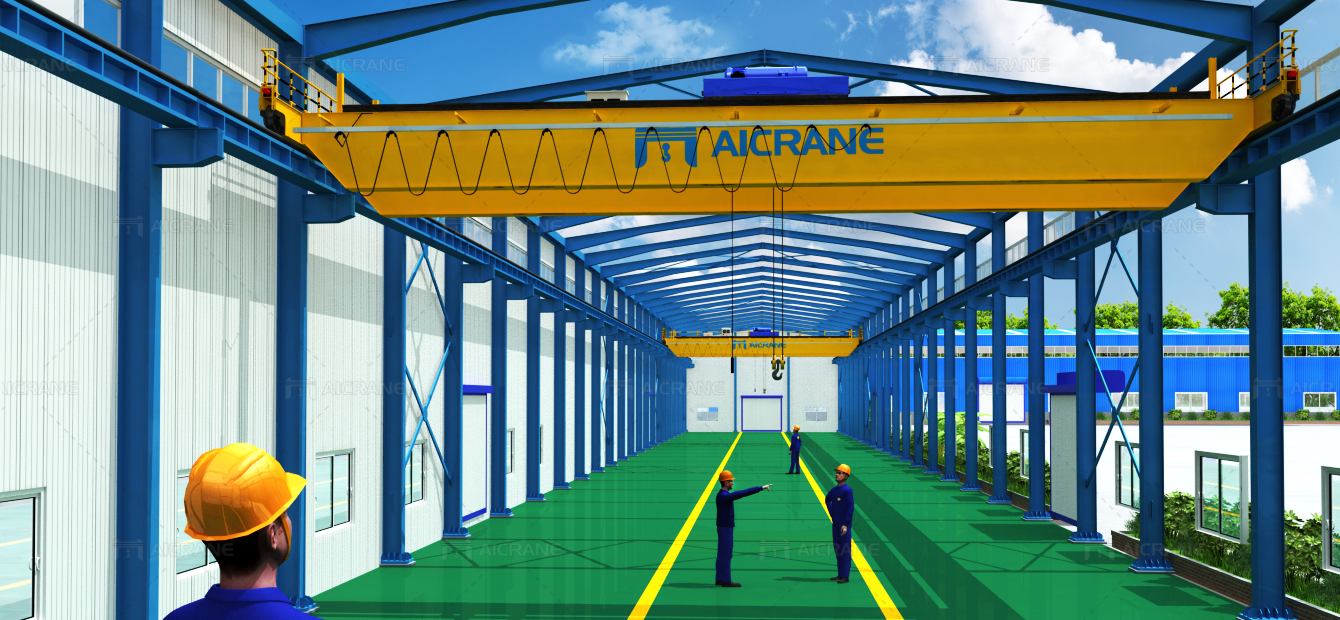
Regular Inspections
Regular inspections are the cornerstone of maintaining the stability of a steel building factory. These inspections help identify potential issues before they escalate into serious problems. Key aspects of an inspection routine include:
Structural Elements: Inspect all structural elements, including beams, columns, trusses, and connections. Look for signs of wear, corrosion, or deformation that could compromise the building's stability.
Roof and Walls: Examine the roof and walls for any damage, leaks, or corrosion. Ensure that the building envelope is intact to prevent water ingress and other environmental damage.
Foundation: Check the foundation for any cracks, settlement, or other signs of distress. A stable foundation is crucial for the overall stability of the building.
Fasteners and Connections: Inspect bolts, welds, and other connections to ensure they are secure. Loose or corroded fasteners can weaken the structure and lead to instability.
Preventive Maintenance
Preventive maintenance is essential to address minor issues before they become major problems. A proactive maintenance schedule includes:
Cleaning and Coating: Regularly clean the steel surfaces to remove dirt, debris, and other contaminants that can cause corrosion. Apply protective coatings to steel elements to prevent rust and extend their lifespan.
Lubrication: Lubricate moving parts such as doors, windows, and mechanical systems to ensure smooth operation and prevent wear.
Sealant Renewal: Reapply sealants and caulking around windows, doors, and joints to maintain a weather-tight seal and prevent moisture intrusion.
Drainage Systems: Maintain and clean gutters, downspouts, and drainage systems to ensure proper water flow and prevent water accumulation that could damage the structure.
Corrosion Control
Corrosion is a significant threat to the stability of steel structures. Implementing effective corrosion control measures is vital:
Galvanization: Use galvanized steel components where possible. The zinc coating provides a protective layer that resists corrosion.
Cathodic Protection: Employ cathodic protection systems to prevent corrosion in buried or submerged steel elements. This technique involves using sacrificial anodes or impressed current to protect the steel.
Environmental Controls: Control environmental factors such as humidity and temperature within the building to reduce the risk of corrosion. Dehumidifiers and proper ventilation can help maintain optimal conditions.
Structural Enhancements
Enhancing the structural integrity of a steel building (https://aicranemachine.com/steel-structure/) factory can prevent instability and extend the building's lifespan. Consider the following enhancements:
Reinforcement: Reinforce critical structural elements with additional steel or other materials to improve their load-bearing capacity.
Retrofitting: Retrofit older buildings with modern materials and techniques to enhance their stability. This may include adding bracing, upgrading connections, or replacing deteriorated components.
Seismic Upgrades: In areas prone to earthquakes, implement seismic upgrades to improve the building's resilience to seismic forces. This can include adding shear walls, bracing, and other reinforcement methods.
Environmental Considerations
Environmental factors play a significant role in the stability of a steel building factory. Addressing these factors can prevent damage and deterioration:
Water Management: Ensure proper drainage and water management around the building to prevent water accumulation and infiltration. Use grading, gutters, and drainage systems to direct water away from the foundation.
Wind Loads: Design and maintain the building to withstand local wind loads. This includes ensuring that the building envelope is secure and that all components are properly anchored.
Thermal Expansion: Account for thermal expansion and contraction in the design and maintenance of the building. Use expansion joints and flexible connections to accommodate temperature changes and prevent stress on the structure.
Operational Practices
The day-to-day operations within the steel building factory can also impact its stability. Implementing safe and efficient operational practices is crucial:
Load Management: Ensure that loads placed on the structure do not exceed its design capacity. Distribute loads evenly and avoid placing excessive weight in concentrated areas.
Equipment Placement: Position heavy equipment and machinery on stable, reinforced areas of the floor to prevent undue stress on the structure.
Safety Protocols: Establish and enforce safety protocols to prevent accidents and damage to the building. This includes proper training for personnel and adherence to safety regulations.
Monitoring and Technology
Leveraging modern technology can enhance the maintenance and monitoring of a steel building factory:
Structural Health Monitoring: Implement structural health monitoring systems that use sensors to track the condition of the building in real time. These systems can detect changes in stress, strain, and other parameters, providing early warning of potential issues.
Building Management Systems: Use building management systems (BMS) to control and monitor environmental conditions, energy usage, and other factors that impact the stability of the building.
Drones and Robotics: Employ drones and robotic systems for inspections and maintenance tasks. These technologies can access hard-to-reach areas and provide detailed assessments of the building's condition.
Documentation and Record Keeping
Maintaining detailed records of inspections, maintenance, and repairs is essential for tracking the building's health and addressing issues promptly:
Inspection Reports: Document all inspection findings, including any identified issues and recommended actions.
Maintenance Logs: Keep detailed logs of all maintenance activities, including cleaning, coating, lubrication, and repairs.
Repair Records: Record all repairs and replacements, including the date, nature of the work, and materials used. This information is valuable for future reference and planning.
Maintaining the stability of a steel building factory is a multifaceted task that requires regular inspections, preventive maintenance, effective corrosion control, structural enhancements, and consideration of environmental and operational factors. Leveraging modern technology and maintaining detailed records further enhances the ability to preserve the structural integrity of the building. By implementing these strategies, industrial operators can ensure the safety, efficiency, and longevity of their steel building factory, ultimately contributing to sustained productivity and operational success. A proactive approach to maintenance not only prevents costly repairs and downtime but also safeguards the well-being of personnel and the overall investment in the facility.
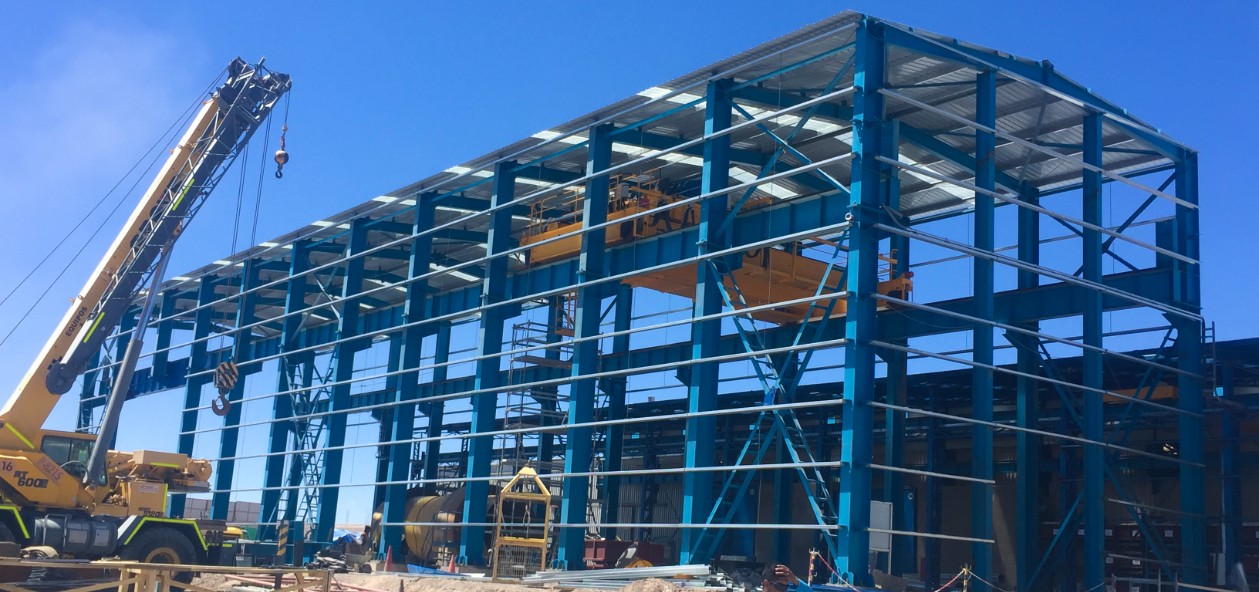
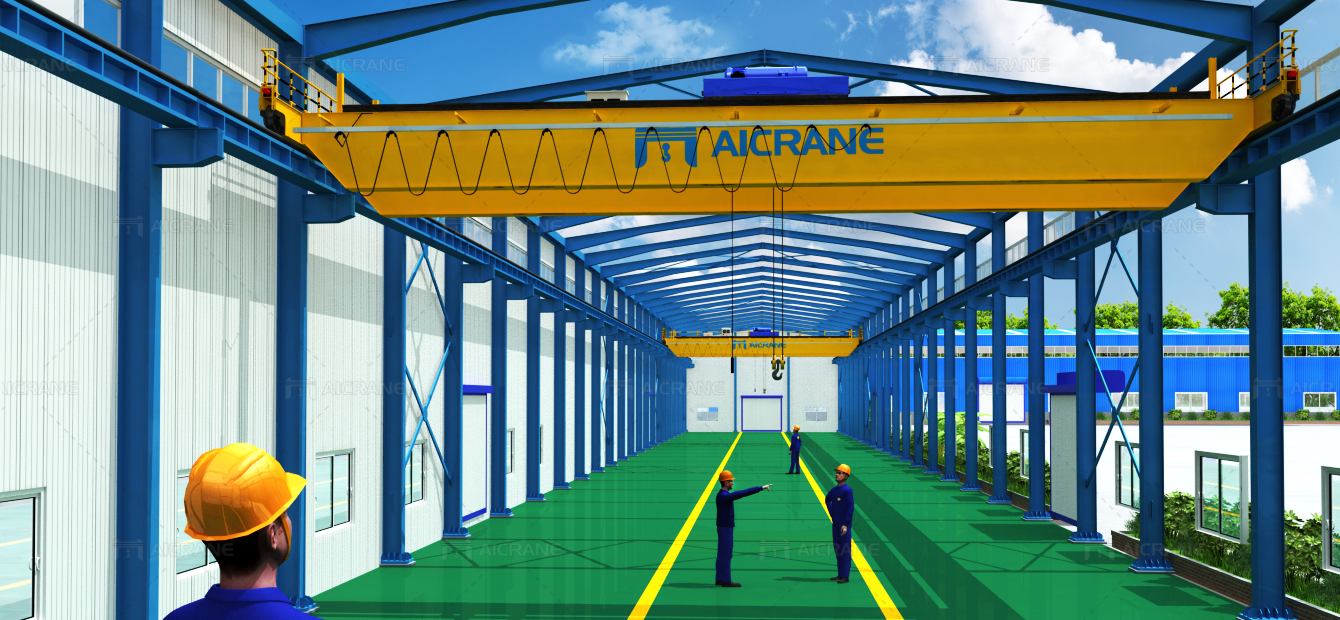
Regular Inspections
Regular inspections are the cornerstone of maintaining the stability of a steel building factory. These inspections help identify potential issues before they escalate into serious problems. Key aspects of an inspection routine include:
Structural Elements: Inspect all structural elements, including beams, columns, trusses, and connections. Look for signs of wear, corrosion, or deformation that could compromise the building's stability.
Roof and Walls: Examine the roof and walls for any damage, leaks, or corrosion. Ensure that the building envelope is intact to prevent water ingress and other environmental damage.
Foundation: Check the foundation for any cracks, settlement, or other signs of distress. A stable foundation is crucial for the overall stability of the building.
Fasteners and Connections: Inspect bolts, welds, and other connections to ensure they are secure. Loose or corroded fasteners can weaken the structure and lead to instability.
Preventive Maintenance
Preventive maintenance is essential to address minor issues before they become major problems. A proactive maintenance schedule includes:
Cleaning and Coating: Regularly clean the steel surfaces to remove dirt, debris, and other contaminants that can cause corrosion. Apply protective coatings to steel elements to prevent rust and extend their lifespan.
Lubrication: Lubricate moving parts such as doors, windows, and mechanical systems to ensure smooth operation and prevent wear.
Sealant Renewal: Reapply sealants and caulking around windows, doors, and joints to maintain a weather-tight seal and prevent moisture intrusion.
Drainage Systems: Maintain and clean gutters, downspouts, and drainage systems to ensure proper water flow and prevent water accumulation that could damage the structure.
Corrosion Control
Corrosion is a significant threat to the stability of steel structures. Implementing effective corrosion control measures is vital:
Galvanization: Use galvanized steel components where possible. The zinc coating provides a protective layer that resists corrosion.
Cathodic Protection: Employ cathodic protection systems to prevent corrosion in buried or submerged steel elements. This technique involves using sacrificial anodes or impressed current to protect the steel.
Environmental Controls: Control environmental factors such as humidity and temperature within the building to reduce the risk of corrosion. Dehumidifiers and proper ventilation can help maintain optimal conditions.
Structural Enhancements
Enhancing the structural integrity of a steel building (https://aicranemachine.com/steel-structure/) factory can prevent instability and extend the building's lifespan. Consider the following enhancements:
Reinforcement: Reinforce critical structural elements with additional steel or other materials to improve their load-bearing capacity.
Retrofitting: Retrofit older buildings with modern materials and techniques to enhance their stability. This may include adding bracing, upgrading connections, or replacing deteriorated components.
Seismic Upgrades: In areas prone to earthquakes, implement seismic upgrades to improve the building's resilience to seismic forces. This can include adding shear walls, bracing, and other reinforcement methods.
Environmental Considerations
Environmental factors play a significant role in the stability of a steel building factory. Addressing these factors can prevent damage and deterioration:
Water Management: Ensure proper drainage and water management around the building to prevent water accumulation and infiltration. Use grading, gutters, and drainage systems to direct water away from the foundation.
Wind Loads: Design and maintain the building to withstand local wind loads. This includes ensuring that the building envelope is secure and that all components are properly anchored.
Thermal Expansion: Account for thermal expansion and contraction in the design and maintenance of the building. Use expansion joints and flexible connections to accommodate temperature changes and prevent stress on the structure.
Operational Practices
The day-to-day operations within the steel building factory can also impact its stability. Implementing safe and efficient operational practices is crucial:
Load Management: Ensure that loads placed on the structure do not exceed its design capacity. Distribute loads evenly and avoid placing excessive weight in concentrated areas.
Equipment Placement: Position heavy equipment and machinery on stable, reinforced areas of the floor to prevent undue stress on the structure.
Safety Protocols: Establish and enforce safety protocols to prevent accidents and damage to the building. This includes proper training for personnel and adherence to safety regulations.
Monitoring and Technology
Leveraging modern technology can enhance the maintenance and monitoring of a steel building factory:
Structural Health Monitoring: Implement structural health monitoring systems that use sensors to track the condition of the building in real time. These systems can detect changes in stress, strain, and other parameters, providing early warning of potential issues.
Building Management Systems: Use building management systems (BMS) to control and monitor environmental conditions, energy usage, and other factors that impact the stability of the building.
Drones and Robotics: Employ drones and robotic systems for inspections and maintenance tasks. These technologies can access hard-to-reach areas and provide detailed assessments of the building's condition.
Documentation and Record Keeping
Maintaining detailed records of inspections, maintenance, and repairs is essential for tracking the building's health and addressing issues promptly:
Inspection Reports: Document all inspection findings, including any identified issues and recommended actions.
Maintenance Logs: Keep detailed logs of all maintenance activities, including cleaning, coating, lubrication, and repairs.
Repair Records: Record all repairs and replacements, including the date, nature of the work, and materials used. This information is valuable for future reference and planning.
Maintaining the stability of a steel building factory is a multifaceted task that requires regular inspections, preventive maintenance, effective corrosion control, structural enhancements, and consideration of environmental and operational factors. Leveraging modern technology and maintaining detailed records further enhances the ability to preserve the structural integrity of the building. By implementing these strategies, industrial operators can ensure the safety, efficiency, and longevity of their steel building factory, ultimately contributing to sustained productivity and operational success. A proactive approach to maintenance not only prevents costly repairs and downtime but also safeguards the well-being of personnel and the overall investment in the facility.
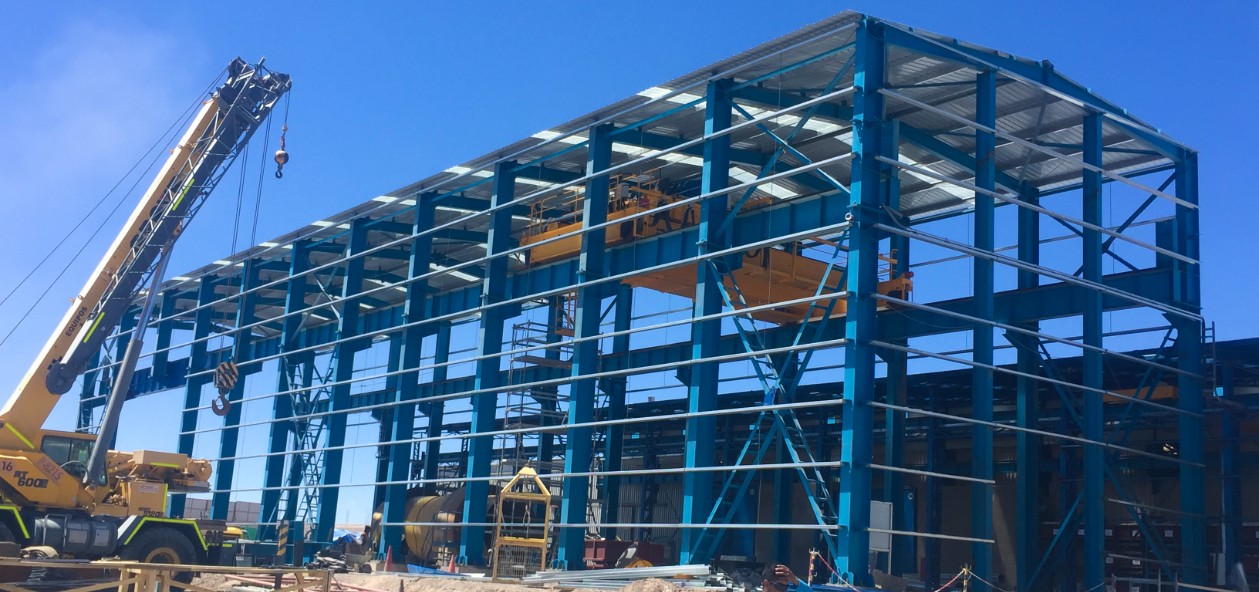