12
0
0
The Impact of Burner Power on Fuel Consumption in Asphalt Mixing Plants
In the asphalt production industry, the efficiency of fuel consumption is crucial for both economic viability and environmental sustainability. One of the key factors influencing fuel consumption is the power of the burners used in asphalt mixing plants. Understanding how different burner powers affect fuel efficiency can help operators optimize their processes, reduce costs, and improve overall performance. This article explores the relationship between burner power and fuel consumption, focusing on user-centered insights.
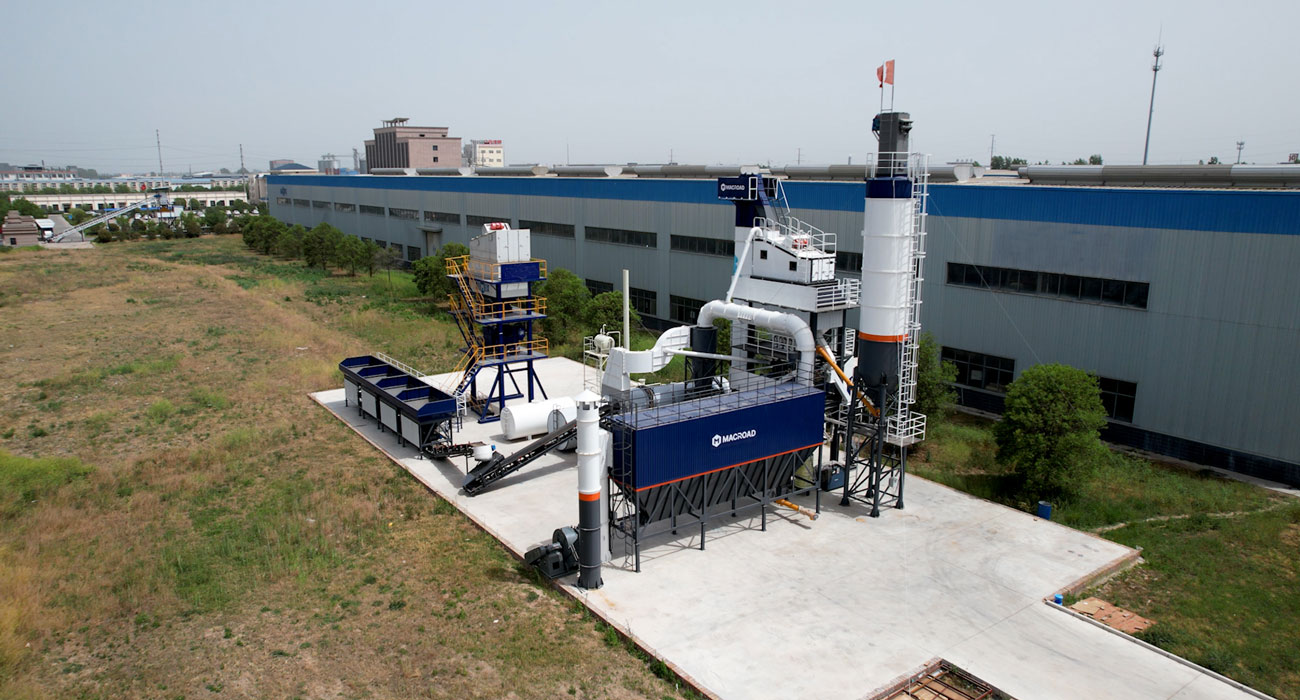
The Role of Burner Power in Fuel Efficiency
Burner power refers to the output capacity of the burner, which directly affects how efficiently fuel is consumed during the asphalt mixing process. Higher-powered burners can generate more heat, allowing for faster heating of aggregates and asphalt. While this can lead to increased production rates, it also raises questions about fuel consumption efficiency.
For example, a fixed asphalt mixing plant equipped with a high-capacity burner may produce asphalt more quickly, but if the burner operates at a power level that exceeds the plant's actual requirements, it can lead to excessive fuel consumption. Conversely, a mobile asphalt plant with a lower-powered burner may consume less fuel overall, but it could also slow down production. Striking the right balance between burner power and production needs is essential for optimizing fuel efficiency.
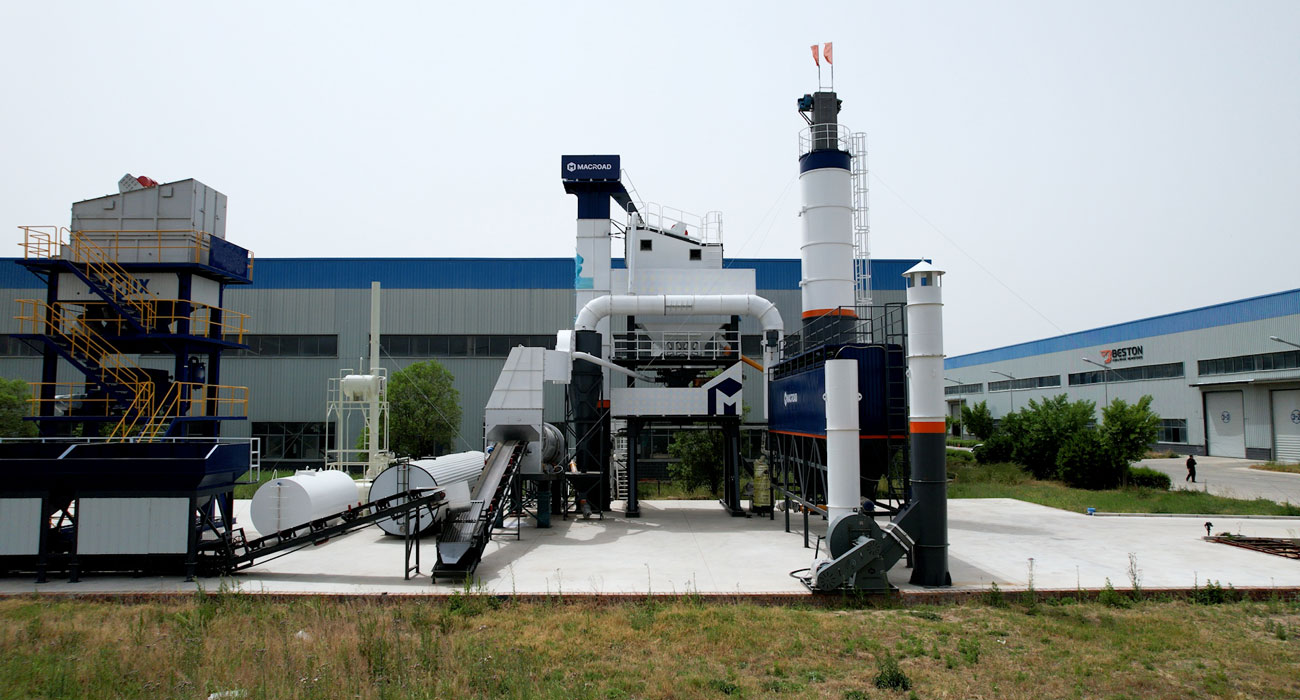
Optimizing Burner Settings for Fuel Consumption
To maximize fuel efficiency, operators should focus on optimizing burner settings. This includes adjusting the air-fuel ratio, burner temperature, and operational parameters based on the specific requirements of the asphalt mix. By fine-tuning these settings, operators can ensure that the burner operates at its most efficient level, minimizing unnecessary fuel consumption.
Additionally, utilizing advanced burner technologies can lead to significant improvements in fuel efficiency. For instance, modern burners often feature automatic controls that adjust combustion parameters in real-time. This not only enhances efficiency but also reduces emissions, contributing to a more environmentally friendly operation. Whether using a strong burner in a stationary setup or a compact burner in a mini asphalt plant, the focus should be on achieving optimal performance while minimizing fuel use.
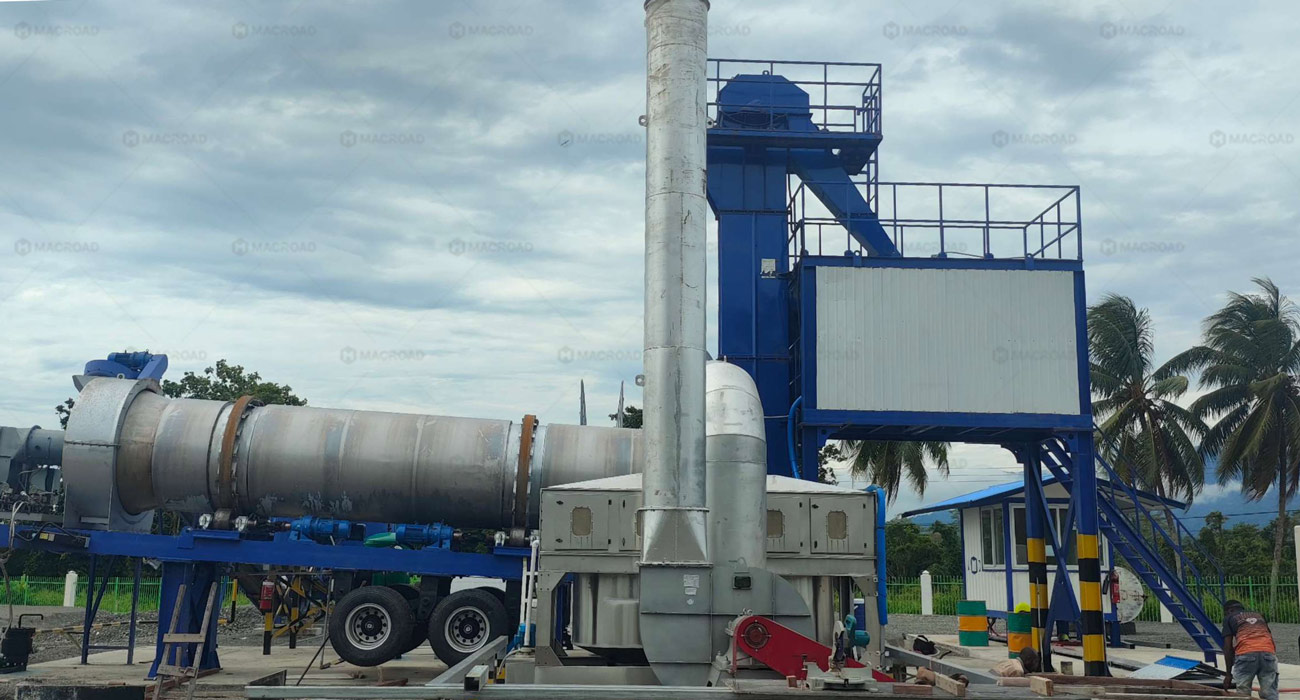
Monitoring and Maintenance for Enhanced Efficiency
Regular monitoring and maintenance of burners are crucial for sustaining fuel efficiency over time. Operators should implement routine checks to ensure that burners are functioning correctly and that there are no blockages or wear that could affect performance. A well-maintained burner will operate more efficiently, reducing fuel consumption and lowering operational costs.
Moreover, integrating monitoring systems that track fuel consumption data can provide valuable insights into burner performance. By analyzing this data, operators can identify patterns and make informed decisions regarding burner adjustments or upgrades. This proactive approach not only enhances fuel efficiency but also contributes to the overall longevity of the asphalt mixing plant.
Conclusion
The power of burners in asphalt mixing plants significantly impacts fuel consumption, making it essential for operators to understand this relationship. By optimizing burner settings, employing advanced technologies, and maintaining equipment, asphalt producers can enhance fuel efficiency, reduce costs, and improve their environmental footprint.
In an era where sustainability and efficiency are paramount, focusing on how burner power affects fuel consumption will be key to successful asphalt production. Whether utilizing a mobile asphalt plant or a fixed facility, understanding these dynamics will enable operators to make informed decisions that support both productivity and sustainability in their operations.
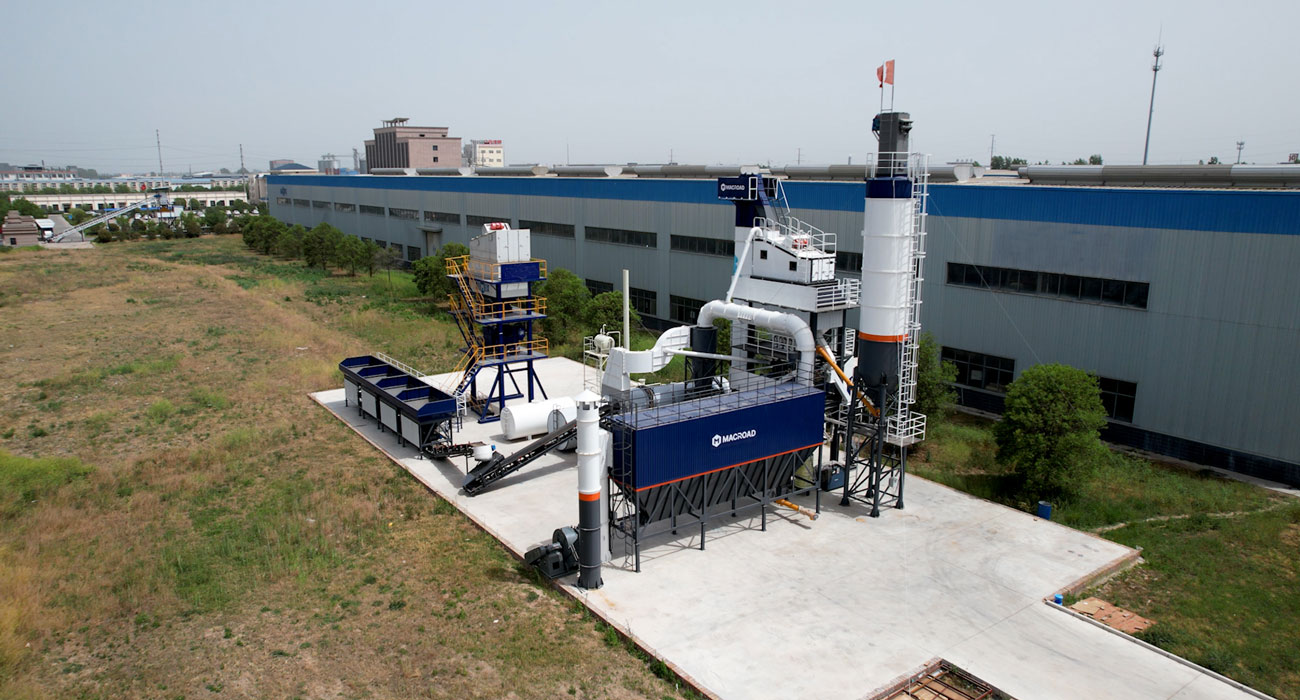
The Role of Burner Power in Fuel Efficiency
Burner power refers to the output capacity of the burner, which directly affects how efficiently fuel is consumed during the asphalt mixing process. Higher-powered burners can generate more heat, allowing for faster heating of aggregates and asphalt. While this can lead to increased production rates, it also raises questions about fuel consumption efficiency.
For example, a fixed asphalt mixing plant equipped with a high-capacity burner may produce asphalt more quickly, but if the burner operates at a power level that exceeds the plant's actual requirements, it can lead to excessive fuel consumption. Conversely, a mobile asphalt plant with a lower-powered burner may consume less fuel overall, but it could also slow down production. Striking the right balance between burner power and production needs is essential for optimizing fuel efficiency.
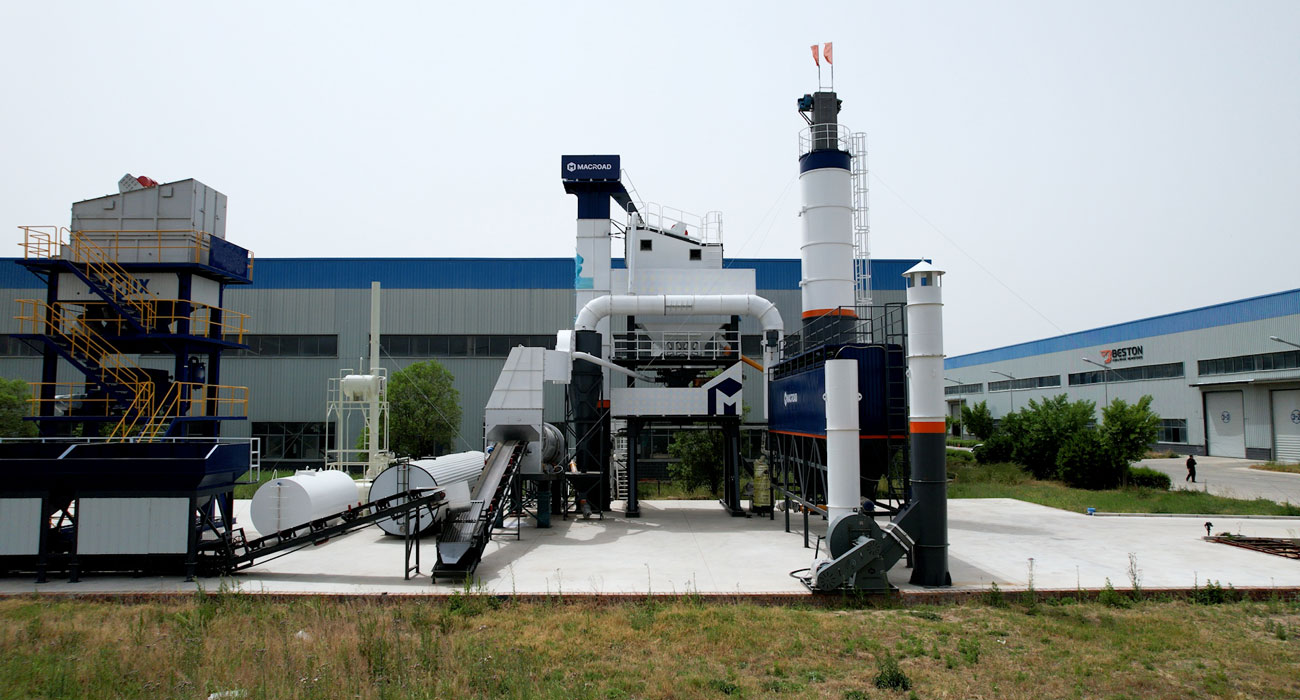
Optimizing Burner Settings for Fuel Consumption
To maximize fuel efficiency, operators should focus on optimizing burner settings. This includes adjusting the air-fuel ratio, burner temperature, and operational parameters based on the specific requirements of the asphalt mix. By fine-tuning these settings, operators can ensure that the burner operates at its most efficient level, minimizing unnecessary fuel consumption.
Additionally, utilizing advanced burner technologies can lead to significant improvements in fuel efficiency. For instance, modern burners often feature automatic controls that adjust combustion parameters in real-time. This not only enhances efficiency but also reduces emissions, contributing to a more environmentally friendly operation. Whether using a strong burner in a stationary setup or a compact burner in a mini asphalt plant, the focus should be on achieving optimal performance while minimizing fuel use.
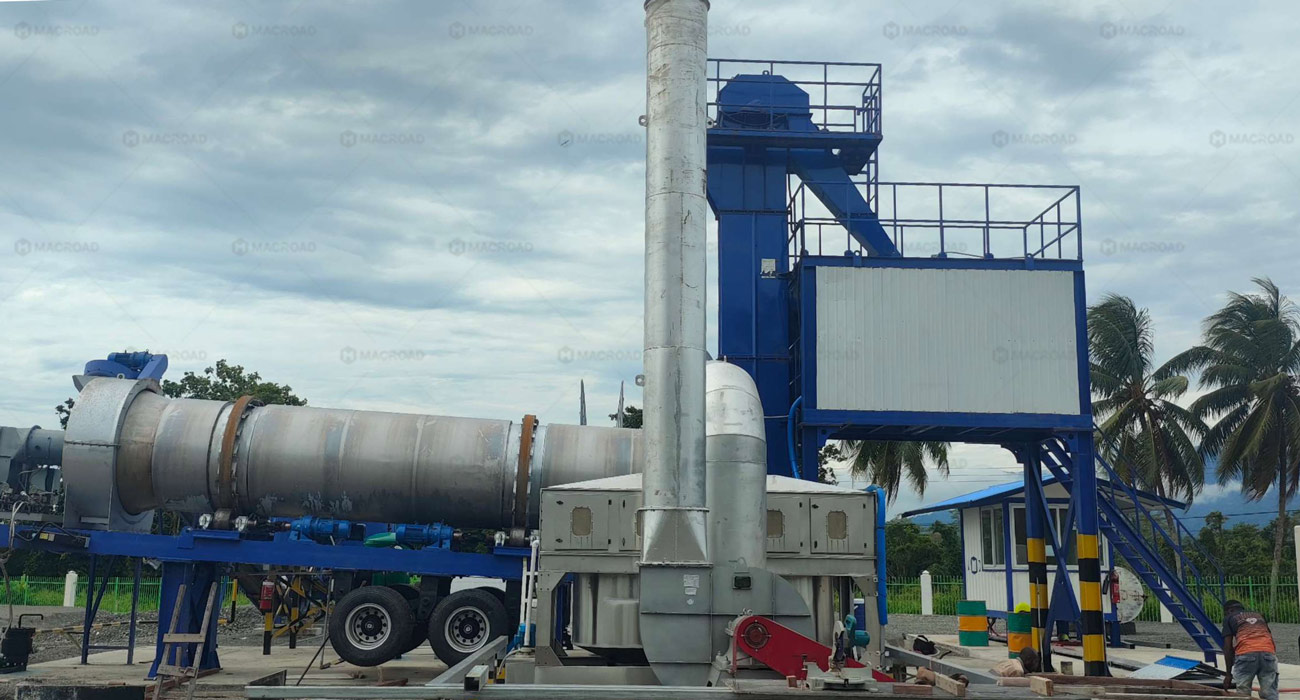
Monitoring and Maintenance for Enhanced Efficiency
Regular monitoring and maintenance of burners are crucial for sustaining fuel efficiency over time. Operators should implement routine checks to ensure that burners are functioning correctly and that there are no blockages or wear that could affect performance. A well-maintained burner will operate more efficiently, reducing fuel consumption and lowering operational costs.
Moreover, integrating monitoring systems that track fuel consumption data can provide valuable insights into burner performance. By analyzing this data, operators can identify patterns and make informed decisions regarding burner adjustments or upgrades. This proactive approach not only enhances fuel efficiency but also contributes to the overall longevity of the asphalt mixing plant.
Conclusion
The power of burners in asphalt mixing plants significantly impacts fuel consumption, making it essential for operators to understand this relationship. By optimizing burner settings, employing advanced technologies, and maintaining equipment, asphalt producers can enhance fuel efficiency, reduce costs, and improve their environmental footprint.
In an era where sustainability and efficiency are paramount, focusing on how burner power affects fuel consumption will be key to successful asphalt production. Whether utilizing a mobile asphalt plant or a fixed facility, understanding these dynamics will enable operators to make informed decisions that support both productivity and sustainability in their operations.