7
0
0
Balancing Project Constraints with Equipment Performance in Asphalt Plant Design
Asphalt plant suppliers face the challenge of balancing project scenario constraints with core equipment performance during the design of customized equipment. Factors such as narrow site spaces and environmental protection zone regulations can complicate the design process, particularly in suburban areas where space is at a premium. This article examines how suppliers navigate these constraints while ensuring production continuity and mixture quality stability, as well as the hidden challenges that arise from such compromises.
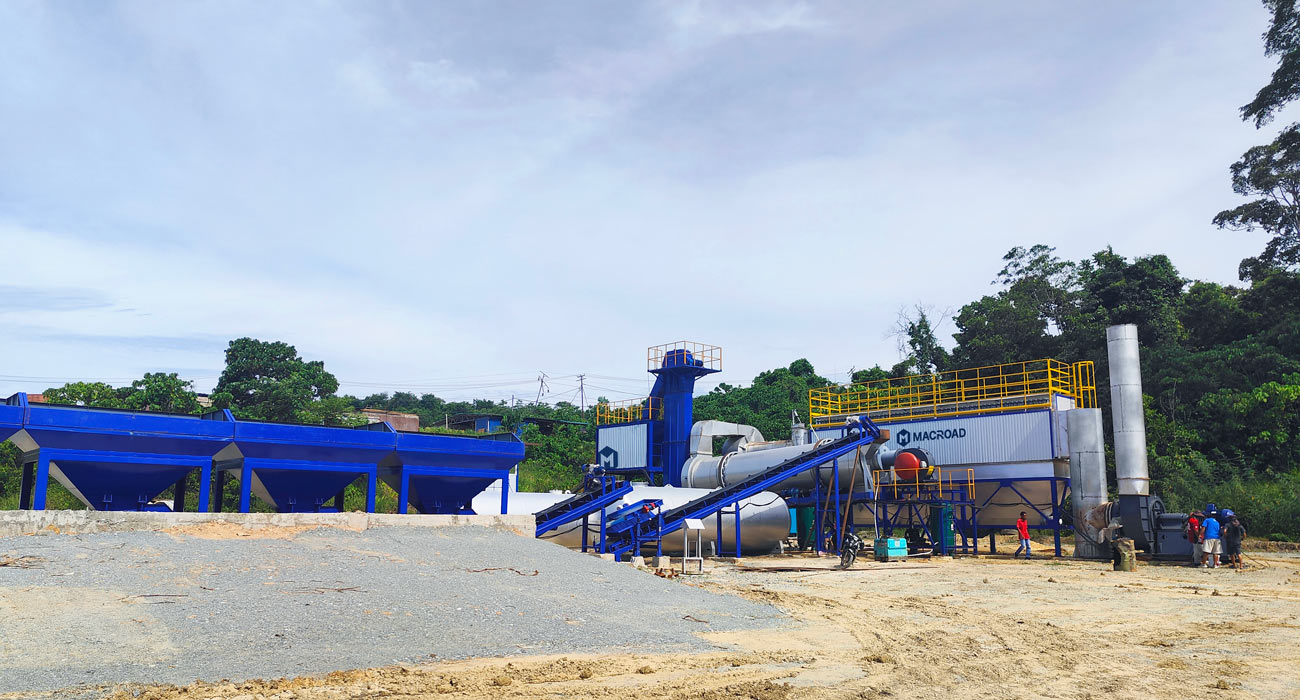
Navigating Space Constraints in Design
In suburban projects where site space is limited, asphalt plant suppliers often adopt compact layout designs to maximize efficiency and functionality. This approach may involve compressing certain auxiliary functional zones, such as aggregate storage and mixing areas, which are essential for maintaining production continuity. While these compact designs can save space and reduce the environmental footprint, they introduce hidden challenges related to equipment reliability.
For instance, when auxiliary functions are condensed, it may lead to increased wear and tear on equipment due to reduced airflow or inadequate access for maintenance. This can compromise the long-term operational reliability of the asphalt plant. Suppliers must therefore carefully consider how to balance compactness with the necessary space for effective equipment operation and maintenance.
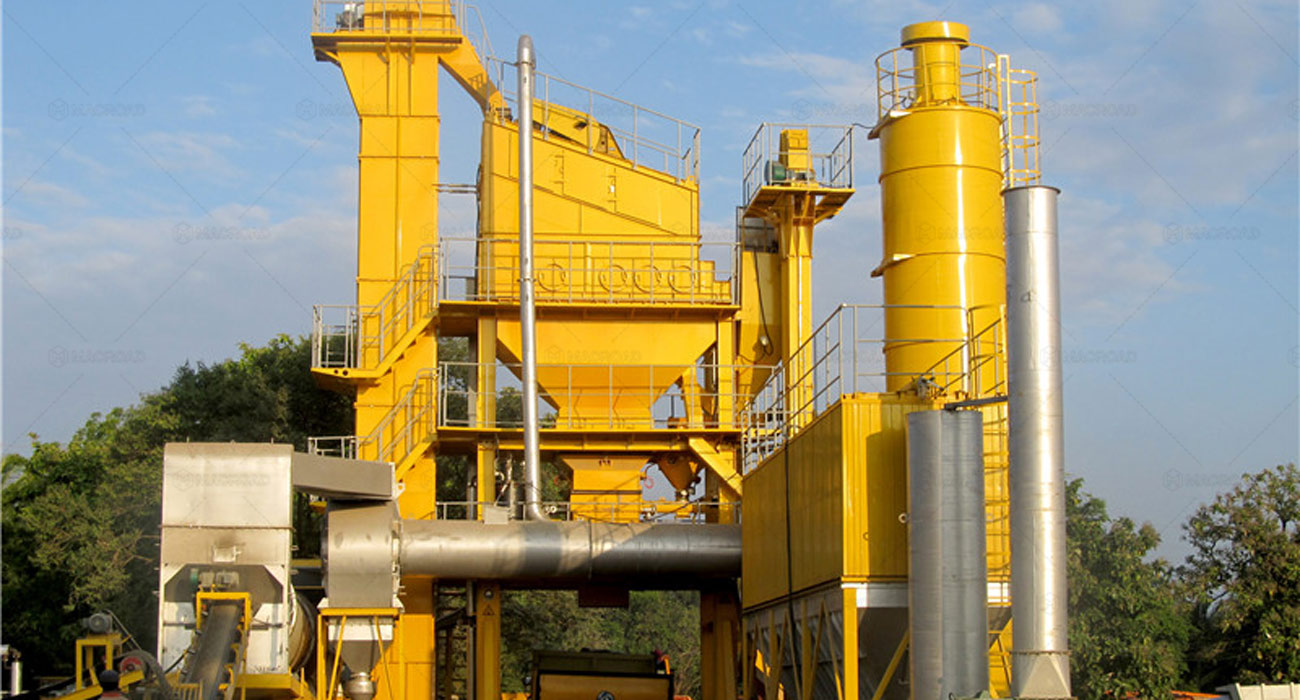
Ensuring Mixture Quality Stability
Another critical aspect of equipment design is ensuring mixture quality stability. In compact setups, the proximity of various components can affect the accuracy of material blending and the control of temperature. When suppliers compress functional zones, they must implement robust systems to monitor and control the mixing process closely. This is particularly important when working with different types of aggregates, as variations can lead to inconsistencies in the final asphalt product.
To mitigate these challenges, suppliers often integrate advanced technologies such as automated monitoring systems and precision mixing controls. These innovations help maintain consistent mixture quality, even within the constraints of a compact design. Asphalt plant suppliers like Macroad are known for their commitment to incorporating such technologies, enhancing both performance and reliability.
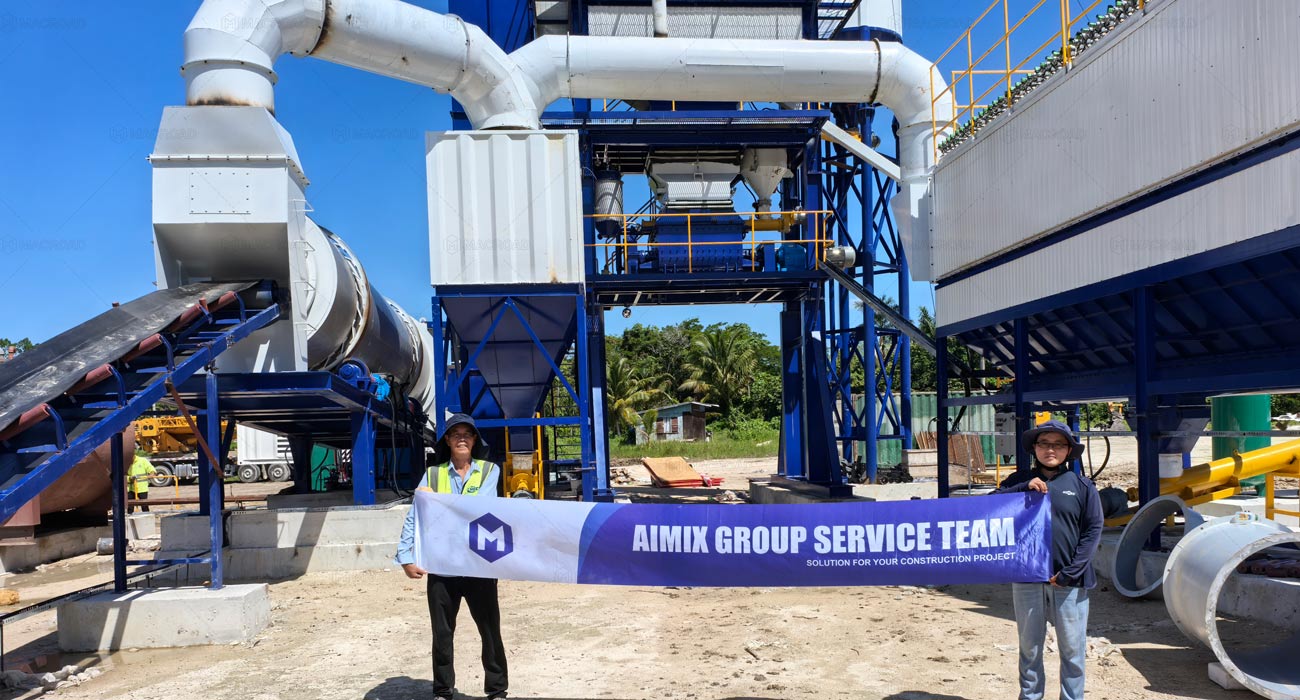
Technical Innovations for Enhanced Performance
To address the contradictions posed by space constraints and the need for high equipment performance, asphalt plant suppliers are increasingly turning to technical innovations. These innovations include modular designs that allow for easier assembly and disassembly, making it possible to adapt to various site conditions. Additionally, suppliers may employ advanced materials that are more durable and resistant to wear, further enhancing the reliability of compact setups.
Moreover, some suppliers are exploring mobile asphalt plants as a solution to space limitations. These units can be transported to different sites, allowing for greater flexibility in production without sacrificing performance. This adaptability is particularly beneficial for small to medium-sized projects that may not warrant a permanent installation.
In conclusion, the balance between project constraints and core equipment performance is a complex challenge for asphalt plant suppliers. By leveraging technical innovations and adopting compact designs, suppliers can effectively navigate these issues while ensuring the reliability and quality of their products. Emerging companies like Macroad are paving the way for new solutions that address the unique needs of the asphalt production industry, offering opportunities for enhanced operational efficiency in the face of growing urbanization and environmental regulations. You can just visit our website to learn more https://macroad.solutions/
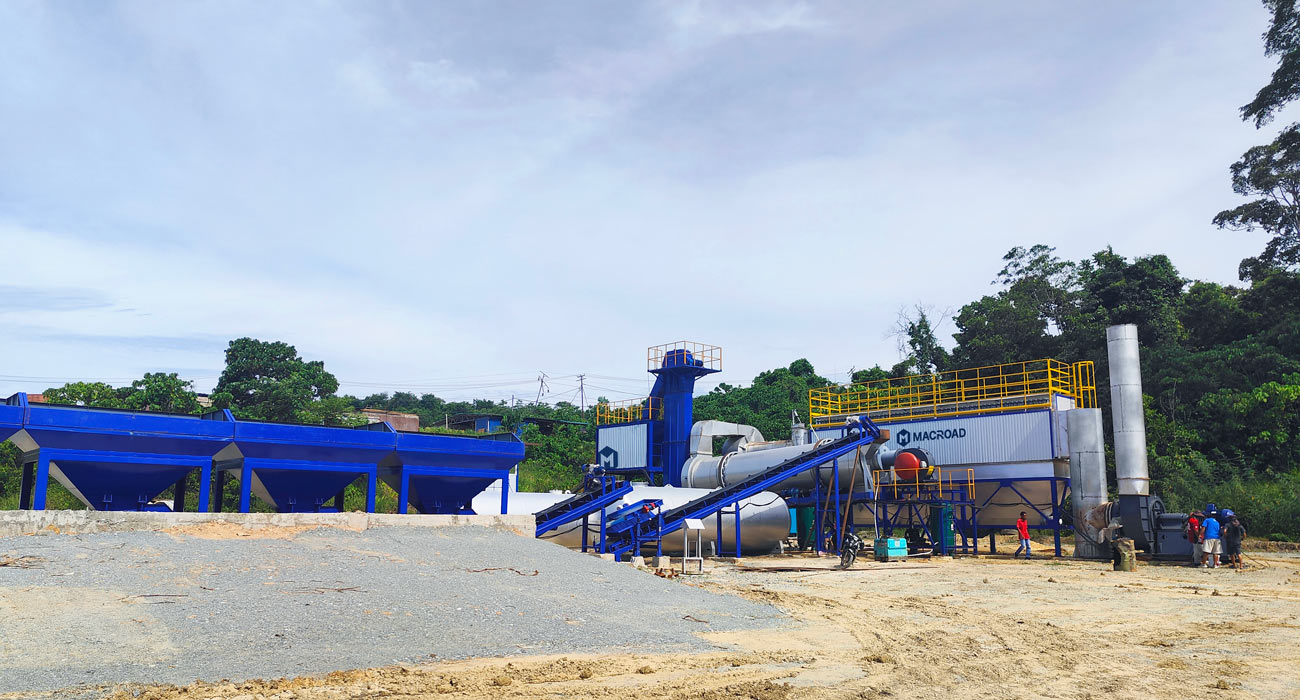
Navigating Space Constraints in Design
In suburban projects where site space is limited, asphalt plant suppliers often adopt compact layout designs to maximize efficiency and functionality. This approach may involve compressing certain auxiliary functional zones, such as aggregate storage and mixing areas, which are essential for maintaining production continuity. While these compact designs can save space and reduce the environmental footprint, they introduce hidden challenges related to equipment reliability.
For instance, when auxiliary functions are condensed, it may lead to increased wear and tear on equipment due to reduced airflow or inadequate access for maintenance. This can compromise the long-term operational reliability of the asphalt plant. Suppliers must therefore carefully consider how to balance compactness with the necessary space for effective equipment operation and maintenance.
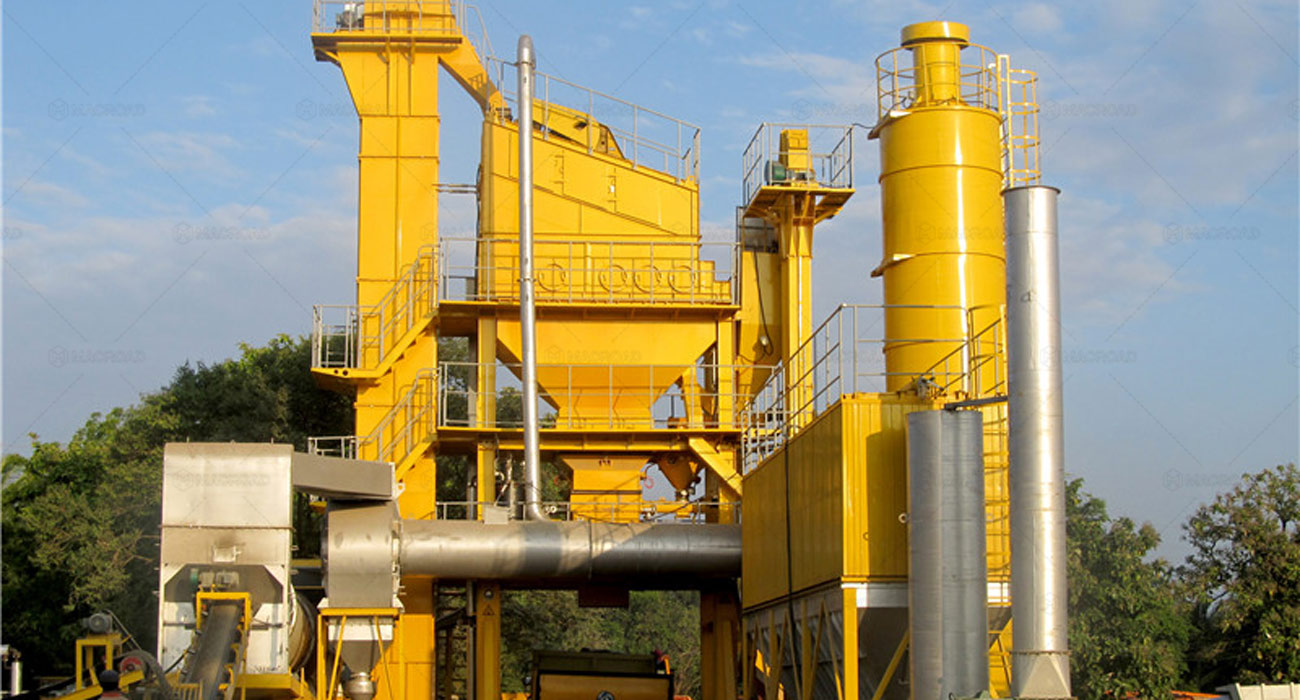
Ensuring Mixture Quality Stability
Another critical aspect of equipment design is ensuring mixture quality stability. In compact setups, the proximity of various components can affect the accuracy of material blending and the control of temperature. When suppliers compress functional zones, they must implement robust systems to monitor and control the mixing process closely. This is particularly important when working with different types of aggregates, as variations can lead to inconsistencies in the final asphalt product.
To mitigate these challenges, suppliers often integrate advanced technologies such as automated monitoring systems and precision mixing controls. These innovations help maintain consistent mixture quality, even within the constraints of a compact design. Asphalt plant suppliers like Macroad are known for their commitment to incorporating such technologies, enhancing both performance and reliability.
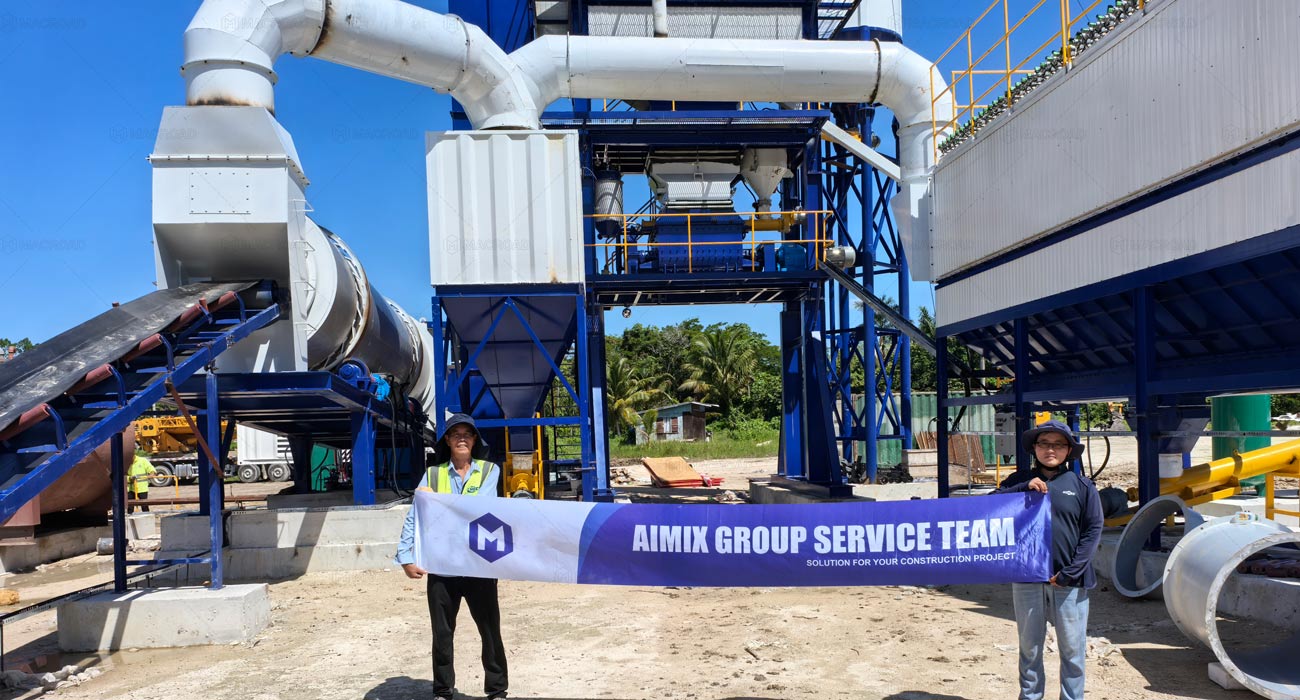
Technical Innovations for Enhanced Performance
To address the contradictions posed by space constraints and the need for high equipment performance, asphalt plant suppliers are increasingly turning to technical innovations. These innovations include modular designs that allow for easier assembly and disassembly, making it possible to adapt to various site conditions. Additionally, suppliers may employ advanced materials that are more durable and resistant to wear, further enhancing the reliability of compact setups.
Moreover, some suppliers are exploring mobile asphalt plants as a solution to space limitations. These units can be transported to different sites, allowing for greater flexibility in production without sacrificing performance. This adaptability is particularly beneficial for small to medium-sized projects that may not warrant a permanent installation.
In conclusion, the balance between project constraints and core equipment performance is a complex challenge for asphalt plant suppliers. By leveraging technical innovations and adopting compact designs, suppliers can effectively navigate these issues while ensuring the reliability and quality of their products. Emerging companies like Macroad are paving the way for new solutions that address the unique needs of the asphalt production industry, offering opportunities for enhanced operational efficiency in the face of growing urbanization and environmental regulations. You can just visit our website to learn more https://macroad.solutions/