28
0
0
Application of Alumina Bubble Brick
4
0
Alumina bubble bricks represent a cutting-edge solution in the realm of refractory materials, offering exceptional thermal insulation and mechanical strength in high-temperature environments. This article explores the various applications and advantages of alumina bubble bricks, highlighting their critical role in industries reliant on robust refractory solutions.
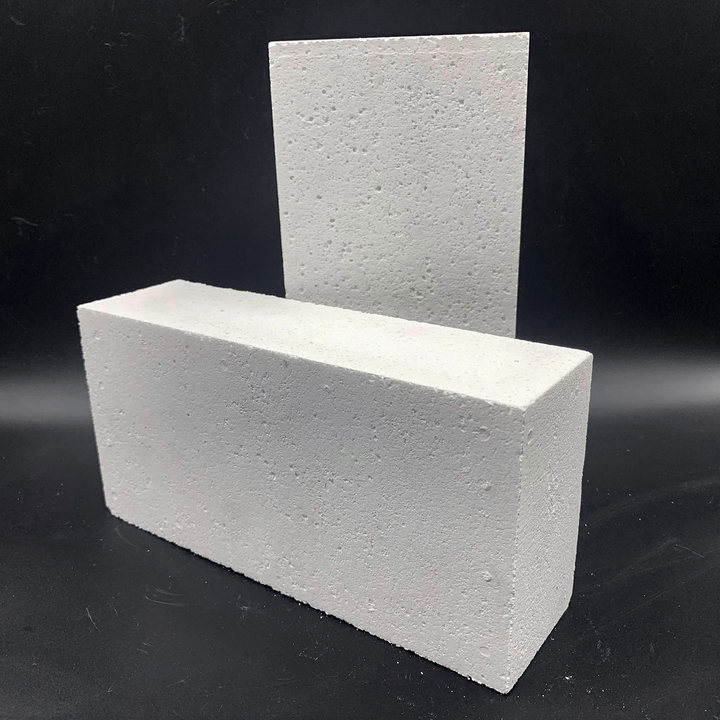
Understanding Alumina Bubble Bricks
Alumina bubble bricks are lightweight refractory products composed primarily of alumina hollow spheres and a binder system. These bricks are characterized by:
High Thermal Stability: Alumina bubble bricks can withstand extreme temperatures up to 1800°C (3272°F) and maintain their structural integrity, making them ideal for applications in furnaces, kilns, and other high-temperature equipment.
Low Thermal Conductivity: The unique structure of white alumina bubble brick, with interconnected hollow spheres, significantly reduces thermal conductivity. This property minimizes heat loss and enhances energy efficiency in industrial processes.
Excellent Insulating Properties: Compared to traditional refractory materials, alumina bubble bricks offer superior insulation, helping to maintain uniform temperatures and optimize heat distribution within furnaces and reactors.
Applications of Alumina Bubble Bricks
a. Iron & Steel Industry:
In steelmaking processes such as ladle linings, alumina bubble bricks provide:
Thermal Insulation: They reduce heat loss during refining and casting operations, improving energy efficiency and reducing operational costs.
Resistance to Chemical Erosion: Alumina bubble bricks withstand chemical reactions and slag corrosion, ensuring prolonged service life and operational reliability.
b. Petrochemical Industry:
For reformers, heaters, and other high-temperature units in petrochemical plants, alumina bubble bricks offer:
Heat Management: Effective insulation properties maintain stable operating temperatures, enhancing process control and product quality.
Durability: Resistance to thermal cycling and chemical attack ensures consistent performance in demanding environments.
c. Non-Ferrous Metals Processing:
Alumina bubble bricks are utilized in smelting furnaces and converters for:
Thermal Efficiency: Facilitating high-temperature operations with minimal heat loss, optimizing energy consumption and reducing environmental impact.
Longevity: Enhanced durability against molten metals and corrosive atmospheres extends the service life of refractory linings.
Installation and Maintenance Considerations
a. Installation Techniques:
Alumina bubble bricks can be installed using standard kiln refractory material practices such as brick laying or gunning, depending on the application requirements.
Proper surface preparation and bonding agents ensure secure adhesion and minimize the risk of thermal bridging.
b. Maintenance Practices:
Regular inspections and preventive maintenance help identify wear, erosion, or thermal shock issues early.
Patching or replacing damaged bricks promptly maintains the integrity of refractory linings and extends their operational lifespan.
Advantages Over Traditional Refractories
Lightweight Construction: Alumina bubble bricks reduce the overall weight of refractory linings, easing structural load and installation efforts.
Energy Efficiency: Lower thermal conductivity translates to reduced heat loss and enhanced process efficiency, yielding significant cost savings over time.
Environmental Benefits: Improved insulation properties contribute to lower greenhouse gas emissions and support sustainable manufacturing practices.
Conclusion
Alumina bubble bricks represent a technological leap in refractory materials, offering unmatched thermal insulation, durability, and energy efficiency across various industrial applications. As industries strive for greater operational efficiency and environmental stewardship, the adoption of alumina bubble bricks continues to play a pivotal role in optimizing high-temperature processes and ensuring sustainable industrial practices. Embracing these advanced refractory solutions not only enhances performance but also underscores a commitment to innovation and resilience in challenging operating environments.
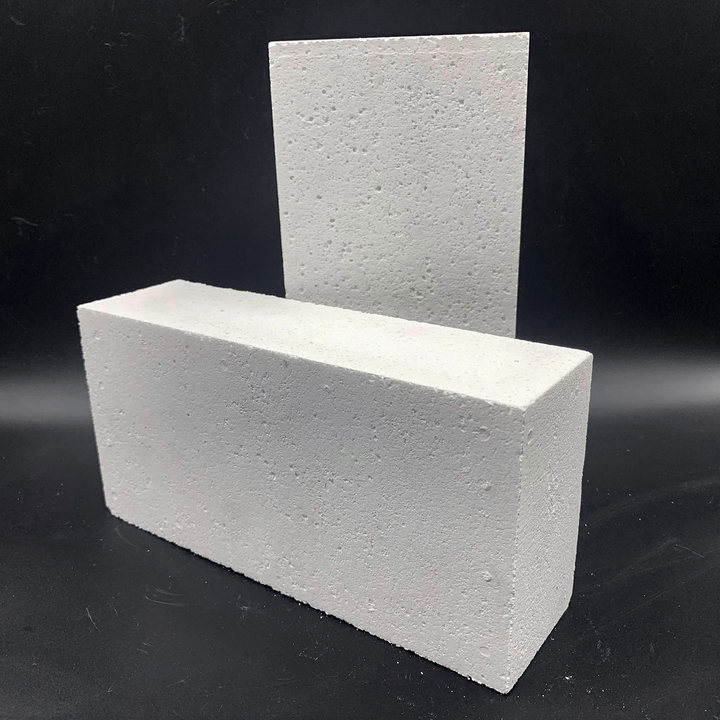
Understanding Alumina Bubble Bricks
Alumina bubble bricks are lightweight refractory products composed primarily of alumina hollow spheres and a binder system. These bricks are characterized by:
High Thermal Stability: Alumina bubble bricks can withstand extreme temperatures up to 1800°C (3272°F) and maintain their structural integrity, making them ideal for applications in furnaces, kilns, and other high-temperature equipment.
Low Thermal Conductivity: The unique structure of white alumina bubble brick, with interconnected hollow spheres, significantly reduces thermal conductivity. This property minimizes heat loss and enhances energy efficiency in industrial processes.
Excellent Insulating Properties: Compared to traditional refractory materials, alumina bubble bricks offer superior insulation, helping to maintain uniform temperatures and optimize heat distribution within furnaces and reactors.
Applications of Alumina Bubble Bricks
a. Iron & Steel Industry:
In steelmaking processes such as ladle linings, alumina bubble bricks provide:
Thermal Insulation: They reduce heat loss during refining and casting operations, improving energy efficiency and reducing operational costs.
Resistance to Chemical Erosion: Alumina bubble bricks withstand chemical reactions and slag corrosion, ensuring prolonged service life and operational reliability.
b. Petrochemical Industry:
For reformers, heaters, and other high-temperature units in petrochemical plants, alumina bubble bricks offer:
Heat Management: Effective insulation properties maintain stable operating temperatures, enhancing process control and product quality.
Durability: Resistance to thermal cycling and chemical attack ensures consistent performance in demanding environments.
c. Non-Ferrous Metals Processing:
Alumina bubble bricks are utilized in smelting furnaces and converters for:
Thermal Efficiency: Facilitating high-temperature operations with minimal heat loss, optimizing energy consumption and reducing environmental impact.
Longevity: Enhanced durability against molten metals and corrosive atmospheres extends the service life of refractory linings.
Installation and Maintenance Considerations
a. Installation Techniques:
Alumina bubble bricks can be installed using standard kiln refractory material practices such as brick laying or gunning, depending on the application requirements.
Proper surface preparation and bonding agents ensure secure adhesion and minimize the risk of thermal bridging.
b. Maintenance Practices:
Regular inspections and preventive maintenance help identify wear, erosion, or thermal shock issues early.
Patching or replacing damaged bricks promptly maintains the integrity of refractory linings and extends their operational lifespan.
Advantages Over Traditional Refractories
Lightweight Construction: Alumina bubble bricks reduce the overall weight of refractory linings, easing structural load and installation efforts.
Energy Efficiency: Lower thermal conductivity translates to reduced heat loss and enhanced process efficiency, yielding significant cost savings over time.
Environmental Benefits: Improved insulation properties contribute to lower greenhouse gas emissions and support sustainable manufacturing practices.
Conclusion
Alumina bubble bricks represent a technological leap in refractory materials, offering unmatched thermal insulation, durability, and energy efficiency across various industrial applications. As industries strive for greater operational efficiency and environmental stewardship, the adoption of alumina bubble bricks continues to play a pivotal role in optimizing high-temperature processes and ensuring sustainable industrial practices. Embracing these advanced refractory solutions not only enhances performance but also underscores a commitment to innovation and resilience in challenging operating environments.