13
0
0
How to Produce a Good Quality 30 Ton Gantry Crane
10
zhengzhou
0
A 30 ton gantry crane is a versatile and powerful piece of equipment commonly used in a variety of industries such as construction, shipping, manufacturing, and warehouses. It is designed to handle heavy loads with precision and efficiency. Producing a high-quality 30 ton gantry crane involves a combination of advanced engineering, quality materials, skilled craftsmanship, and rigorous testing. In this article, we will explore the critical aspects involved in producing a top-tier 30 ton gantry crane, from design and material selection to manufacturing processes and quality control.
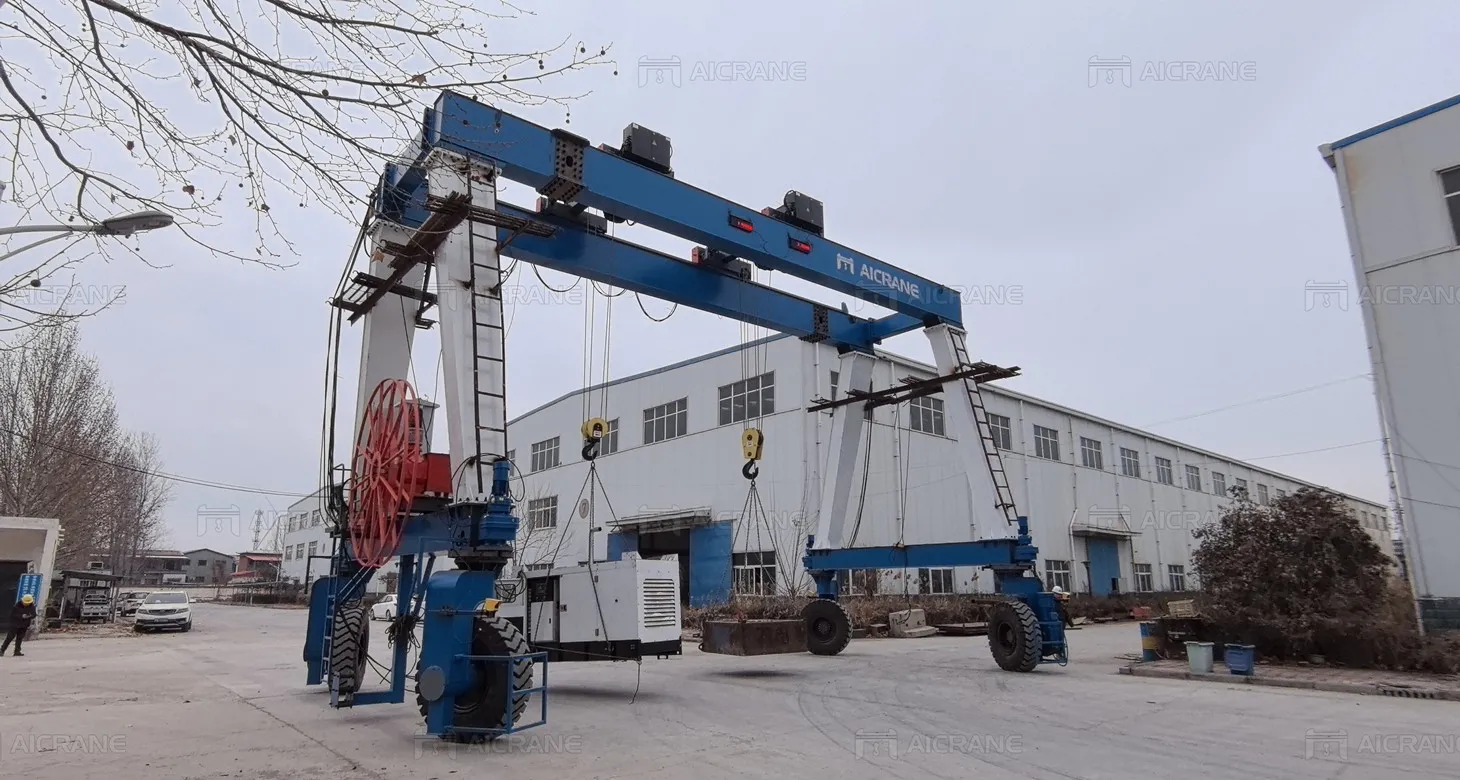
Design and Engineering of a 30 Ton Gantry Crane
The first step in producing a high-quality 30 ton gantry crane begins with the design and engineering phase. The design process must take into account several factors, including the operational requirements, load capacity, working environment, and safety considerations.
a. Load Capacity and Structural Design
The structural design of a 30 ton gantry crane is critical to ensuring that it can safely handle the intended load. Engineers must perform detailed calculations to ensure that the crane's components, such as the main beams, support legs, and cross girder, are capable of withstanding the dynamic and static loads imposed by a 30-ton capacity. Finite Element Analysis (FEA) is often used during the design phase to simulate the performance of the crane under various load conditions and identify potential weak points in the structure.
b. Customization Based on Application
A good-quality 30 ton gantry crane must also be designed with the specific application in mind. Different industries have varying requirements for their gantry cranes. For example, a crane used in a port for container handling may need different specifications than one used in a manufacturing plant for moving heavy machinery. Therefore, the crane's dimensions, lifting speed, span, and height should be customized based on the intended use and environmental factors such as indoor or outdoor operations.
c. Safety Features
Safety is a top priority when designing a gantry crane. Engineers must incorporate essential safety features such as overload protection, anti-collision systems, limit switches, and emergency stop mechanisms. These features not only protect the crane and its load but also ensure the safety of operators and other personnel working around the crane.
Material Selection for a 30 Ton Gantry Crane
The quality of materials used in the construction of a 30 ton gantry crane is a key factor in determining its overall performance, durability, and lifespan. High-quality materials help ensure that the crane can handle heavy loads without deformation or failure.
a. High-Strength Steel
The main structural components of the crane, such as the girders, legs, and hoists, are typically made from high-strength steel. This material offers the necessary tensile strength to support the 30-ton load without bending or buckling. Additionally, using corrosion-resistant steel or applying anti-corrosion coatings can significantly extend the crane's life, especially if it is used in outdoor or harsh environments.
b. High-Quality Motors and Electrical Components
A 30 ton gantry crane relies on motors to drive the hoist, trolley, and gantry movement. These motors must be of high quality to ensure smooth and efficient operation. Low-voltage, high-torque motors are often used for lifting heavy loads with precision. In addition, the electrical components, including control panels, wiring, and sensors, should be durable and resistant to wear and tear.
c. Durable Mechanical Components
The mechanical components, such as gears, shafts, and bearings, must be made from durable materials to withstand the stresses imposed by the heavy lifting operations. Using hardened steel for gears and high-quality lubricants can reduce friction and wear, ensuring long-term reliable operation.
Manufacturing Process of a 30 Ton Gantry Crane
Once the design is finalized and the materials are selected, the next step is the manufacturing process. A well-structured manufacturing process is essential to produce a high-quality 30 ton gantry crane.
a. Precision Fabrication
The fabrication of a gantry crane involves cutting, welding, and assembling various components, including the main beams, legs, hoist trolley, and other structural parts. High-precision cutting techniques, such as laser cutting or CNC (Computer Numerical Control) machines, should be used to ensure that all components are cut to the exact dimensions specified in the design. Precise fabrication is important for maintaining the structural integrity and alignment of the crane.
b. Welding Quality
Welding is a critical process in the construction of a 30 ton gantry crane, as it joins the structural components together. The quality of the welds directly impacts the strength and durability of the crane. Skilled welders must ensure that the welds are strong, free from defects, and meet industry standards. Non-destructive testing methods, such as ultrasonic or radiographic testing, can be used to inspect the welds and ensure there are no hidden flaws.
c. Assembly and Installation
Once the individual components are fabricated and welded, the crane is assembled. This involves attaching the hoist, trolley, motors, and electrical components to the main structure. During assembly, all mechanical and electrical systems must be properly aligned and calibrated to ensure smooth operation.
Testing and Quality Control
A high-quality 30 ton gantry crane must undergo rigorous testing and quality control procedures before it is delivered to the customer. Testing ensures that the crane meets safety and performance standards.
a. Load Testing
Load testing is a critical part of the quality control process. The crane is tested with a load that is 125% of its rated capacity, or 37.5 tons, to ensure that it can safely handle the maximum intended load. This test helps identify any potential weaknesses in the crane's structure or components.
b. Functional Testing
In addition to load testing, the crane must undergo functional tests to verify that all mechanical and electrical systems are operating correctly. This includes testing the hoist and trolley movement, lifting speed, braking systems, and control functions. Any issues identified during testing must be addressed before the crane is deemed ready for use.
c. Compliance with Standards
A good-quality 30 ton gantry crane must comply with relevant industry standards and regulations, such as ISO, ANSI, or CE certifications. Compliance ensures that the crane meets safety, performance, and environmental standards, providing peace of mind to the customer.
After-Sales Support and Maintenance
Producing a high-quality 30 ton gantry crane does not end with the manufacturing process. Providing comprehensive after-sales support, including installation, training, and maintenance, is essential to ensuring long-term customer satisfaction.
a. Installation Services
A reputable gantry crane manufacturer like Aicrane will offer professional installation services to ensure that the crane is installed correctly and safely at the customer's site. Proper installation is critical to the crane's performance and safety.
b. Operator Training
Training the crane operators on how to use the crane safely and efficiently is important. A good manufacturer will provide training on how to operate the crane, perform routine inspections, and carry out basic maintenance tasks.
c. Maintenance and Spare Parts
Regular maintenance is necessary to keep the 30 ton gantry crane in optimal working condition. The manufacturer should offer a maintenance plan and provide access to spare parts to ensure that any worn-out components can be replaced promptly.
Producing a high-quality 30 ton gantry crane involves a combination of meticulous design, careful material selection, precise manufacturing, and rigorous testing. By focusing on each of these aspects, manufacturers can ensure that their cranes are reliable, safe, and capable of handling the demanding tasks required in various industries. Additionally, providing strong after-sales support, including installation, training, and maintenance, ensures that customers get the most value out of their investment in a 30 ton gantry crane.
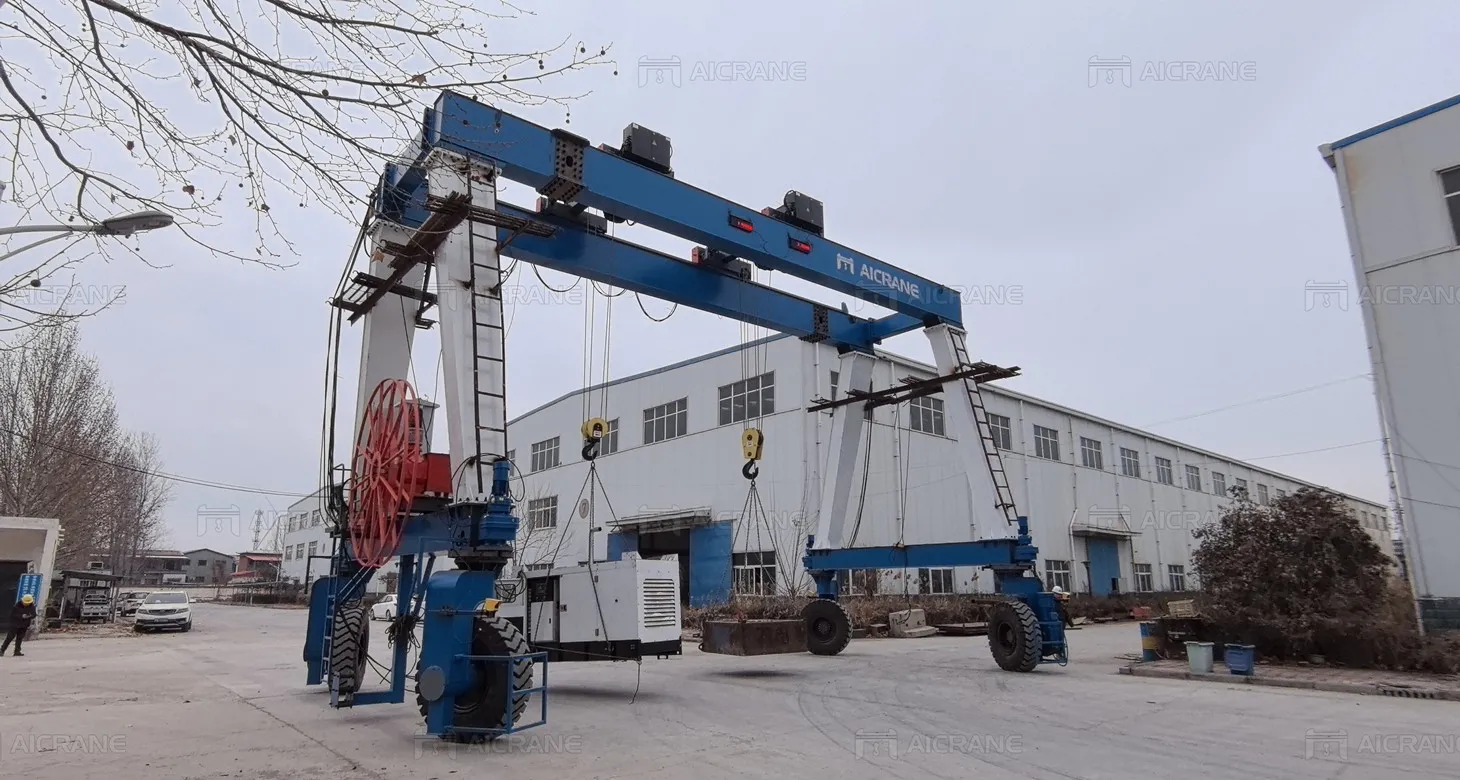
Design and Engineering of a 30 Ton Gantry Crane
The first step in producing a high-quality 30 ton gantry crane begins with the design and engineering phase. The design process must take into account several factors, including the operational requirements, load capacity, working environment, and safety considerations.
a. Load Capacity and Structural Design
The structural design of a 30 ton gantry crane is critical to ensuring that it can safely handle the intended load. Engineers must perform detailed calculations to ensure that the crane's components, such as the main beams, support legs, and cross girder, are capable of withstanding the dynamic and static loads imposed by a 30-ton capacity. Finite Element Analysis (FEA) is often used during the design phase to simulate the performance of the crane under various load conditions and identify potential weak points in the structure.
b. Customization Based on Application
A good-quality 30 ton gantry crane must also be designed with the specific application in mind. Different industries have varying requirements for their gantry cranes. For example, a crane used in a port for container handling may need different specifications than one used in a manufacturing plant for moving heavy machinery. Therefore, the crane's dimensions, lifting speed, span, and height should be customized based on the intended use and environmental factors such as indoor or outdoor operations.
c. Safety Features
Safety is a top priority when designing a gantry crane. Engineers must incorporate essential safety features such as overload protection, anti-collision systems, limit switches, and emergency stop mechanisms. These features not only protect the crane and its load but also ensure the safety of operators and other personnel working around the crane.
Material Selection for a 30 Ton Gantry Crane
The quality of materials used in the construction of a 30 ton gantry crane is a key factor in determining its overall performance, durability, and lifespan. High-quality materials help ensure that the crane can handle heavy loads without deformation or failure.
a. High-Strength Steel
The main structural components of the crane, such as the girders, legs, and hoists, are typically made from high-strength steel. This material offers the necessary tensile strength to support the 30-ton load without bending or buckling. Additionally, using corrosion-resistant steel or applying anti-corrosion coatings can significantly extend the crane's life, especially if it is used in outdoor or harsh environments.
b. High-Quality Motors and Electrical Components
A 30 ton gantry crane relies on motors to drive the hoist, trolley, and gantry movement. These motors must be of high quality to ensure smooth and efficient operation. Low-voltage, high-torque motors are often used for lifting heavy loads with precision. In addition, the electrical components, including control panels, wiring, and sensors, should be durable and resistant to wear and tear.
c. Durable Mechanical Components
The mechanical components, such as gears, shafts, and bearings, must be made from durable materials to withstand the stresses imposed by the heavy lifting operations. Using hardened steel for gears and high-quality lubricants can reduce friction and wear, ensuring long-term reliable operation.
Manufacturing Process of a 30 Ton Gantry Crane
Once the design is finalized and the materials are selected, the next step is the manufacturing process. A well-structured manufacturing process is essential to produce a high-quality 30 ton gantry crane.
a. Precision Fabrication
The fabrication of a gantry crane involves cutting, welding, and assembling various components, including the main beams, legs, hoist trolley, and other structural parts. High-precision cutting techniques, such as laser cutting or CNC (Computer Numerical Control) machines, should be used to ensure that all components are cut to the exact dimensions specified in the design. Precise fabrication is important for maintaining the structural integrity and alignment of the crane.
b. Welding Quality
Welding is a critical process in the construction of a 30 ton gantry crane, as it joins the structural components together. The quality of the welds directly impacts the strength and durability of the crane. Skilled welders must ensure that the welds are strong, free from defects, and meet industry standards. Non-destructive testing methods, such as ultrasonic or radiographic testing, can be used to inspect the welds and ensure there are no hidden flaws.
c. Assembly and Installation
Once the individual components are fabricated and welded, the crane is assembled. This involves attaching the hoist, trolley, motors, and electrical components to the main structure. During assembly, all mechanical and electrical systems must be properly aligned and calibrated to ensure smooth operation.
Testing and Quality Control
A high-quality 30 ton gantry crane must undergo rigorous testing and quality control procedures before it is delivered to the customer. Testing ensures that the crane meets safety and performance standards.
a. Load Testing
Load testing is a critical part of the quality control process. The crane is tested with a load that is 125% of its rated capacity, or 37.5 tons, to ensure that it can safely handle the maximum intended load. This test helps identify any potential weaknesses in the crane's structure or components.
b. Functional Testing
In addition to load testing, the crane must undergo functional tests to verify that all mechanical and electrical systems are operating correctly. This includes testing the hoist and trolley movement, lifting speed, braking systems, and control functions. Any issues identified during testing must be addressed before the crane is deemed ready for use.
c. Compliance with Standards
A good-quality 30 ton gantry crane must comply with relevant industry standards and regulations, such as ISO, ANSI, or CE certifications. Compliance ensures that the crane meets safety, performance, and environmental standards, providing peace of mind to the customer.
After-Sales Support and Maintenance
Producing a high-quality 30 ton gantry crane does not end with the manufacturing process. Providing comprehensive after-sales support, including installation, training, and maintenance, is essential to ensuring long-term customer satisfaction.
a. Installation Services
A reputable gantry crane manufacturer like Aicrane will offer professional installation services to ensure that the crane is installed correctly and safely at the customer's site. Proper installation is critical to the crane's performance and safety.
b. Operator Training
Training the crane operators on how to use the crane safely and efficiently is important. A good manufacturer will provide training on how to operate the crane, perform routine inspections, and carry out basic maintenance tasks.
c. Maintenance and Spare Parts
Regular maintenance is necessary to keep the 30 ton gantry crane in optimal working condition. The manufacturer should offer a maintenance plan and provide access to spare parts to ensure that any worn-out components can be replaced promptly.
Producing a high-quality 30 ton gantry crane involves a combination of meticulous design, careful material selection, precise manufacturing, and rigorous testing. By focusing on each of these aspects, manufacturers can ensure that their cranes are reliable, safe, and capable of handling the demanding tasks required in various industries. Additionally, providing strong after-sales support, including installation, training, and maintenance, ensures that customers get the most value out of their investment in a 30 ton gantry crane.
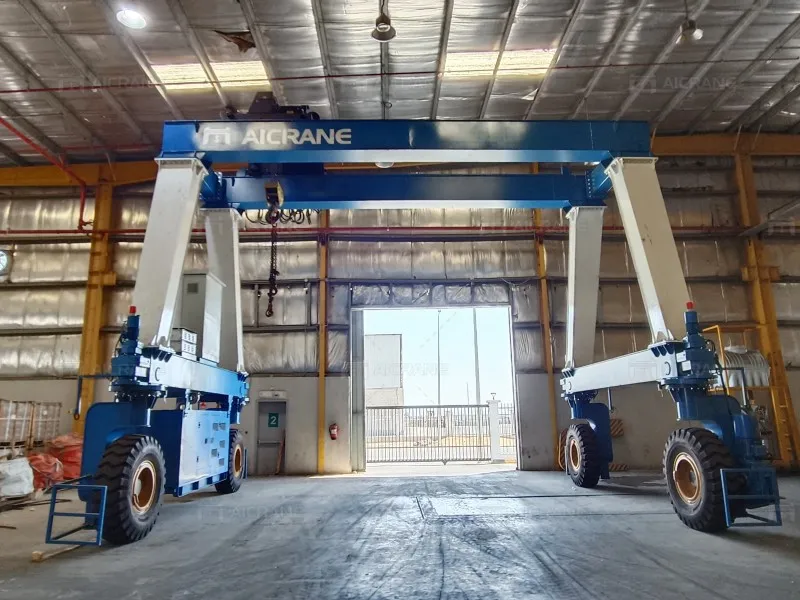