6
0
0
Choosing the Right Ladle Crane Capacity for Your Foundry
5
0
Ladle cranes are essential pieces of equipment in steel production facilities, foundries, and metal casting operations. These cranes are specifically designed for handling molten metal in ladles, transporting them from one part of the production line to another. Given the extreme heat and heavy loads they must handle, choosing the right ladle crane capacity is a critical decision for ensuring safety, efficiency, and productivity in your foundry. This article explores the key factors to consider when selecting the appropriate ladle crane capacity, addressing both operational and safety concerns.
Understanding Ladle Crane Capacities
Ladle crane capacity refers to the maximum weight the crane can safely lift and transport. In a foundry, this typically means the total weight of the ladle filled with molten metal, along with any additional rigging or attachments used for secure handling. Ladle crane capacities can range from several tons to over 500 tons, depending on the size and requirements of the foundry.
Key Considerations When Selecting Ladle Crane Capacity
Choosing the correct crane capacity for your foundry depends on various operational factors, including the volume of molten metal handled, safety regulations, and production demands. Here are the main considerations to keep in mind:
1. Weight of the Ladle and Molten Metal
The most critical factor in determining the capacity of a ladle crane is the total weight of the ladle and its molten metal content. You need to calculate the maximum weight the crane will lift during regular operations. This includes:
For example, if your foundry uses a ladle that holds 50 tons of molten metal and the ladle itself weighs 10 tons, you’ll need a crane with at least a 60-ton capacity. It is crucial to consider a margin of safety above this capacity to account for fluctuations in load and ensure the crane is not operating at its absolute maximum capacity at all times.
2. Production Scale and Future Growth
Another key consideration is your current and future production scale. It’s important to select a ladle crane that meets not only your present needs but also accommodates potential growth in production capacity. If your foundry is planning to expand or increase production output in the future, opting for a slightly higher crane capacity now may save you from costly upgrades or replacements later on.
For instance, if your foundry is currently handling 50-ton ladles but expects to increase molten metal output in the coming years, it may be prudent to choose a crane with a capacity of 60 or 70 tons. This approach provides flexibility for future growth without compromising efficiency or safety. To learn more about cranes for foundry, click here https://aicraneliftingsolution.com/overhead-cranes/foundry/
3. Work Duty and Operating Conditions
Ladle cranes are exposed to demanding working conditions, including high temperatures, dust, and intensive use. The duty cycle of the crane—how frequently it will be in operation and the intensity of its use—is an important factor when selecting capacity.
Ladle cranes are classified according to duty ratings such as A6, A7, or A8 (based on international standards), with higher ratings suitable for more demanding environments. For example:
If your foundry operates multiple shifts or has a high production demand, selecting a ladle crane with a higher duty rating and greater capacity will ensure reliable performance over time without frequent downtime or repairs.
4. Safety Requirements and Regulations
Safety is paramount when handling molten metal. Ladle cranes operate in hazardous environments, and overloading them can lead to catastrophic accidents, including the spilling of molten metal or crane failure. To minimize risks, it is important to choose a crane with a capacity that comfortably exceeds your maximum operational load.
In addition, national and international safety standards, such as OSHA (Occupational Safety and Health Administration) or CE (Conformité Européenne) marking for machinery, must be strictly adhered to. Most foundries incorporate at least a 10-15% safety margin into their capacity calculations to prevent overload conditions.
5. Crane Type and Configuration
Ladle cranes come in various types and configurations, including single-girder and double-girder designs, each with different load capacities and operational characteristics. Typically, double-girder cranes offer higher lifting capacities and are more stable for handling heavy loads, making them ideal for larger foundries with high production demands.
Additionally, some ladle cranes are equipped with features such as:
These additional features should also be factored in when determining the appropriate crane capacity, as they can impact the overall weight the crane must handle.
6. Maintenance and Durability
Durability and ease of maintenance are critical when selecting any crane for a foundry, especially given the challenging operating conditions. Cranes operating in high-heat environments with exposure to molten metal must be built from high-strength, heat-resistant materials. Furthermore, regular maintenance checks should be part of the operational schedule to ensure the crane operates safely at full capacity.
When choosing the right crane capacity, you’ll want to consider the manufacturer's reputation for durability and after-sales support. Investing in a crane that offers easy access to replacement parts, service technicians, and maintenance packages will reduce long-term operational costs and minimize downtime.
Conclusion
Choosing the right ladle crane capacity for your foundry is a decision that directly impacts your production efficiency, safety, and operational success. By considering the total weight of the ladle and molten metal, production scale, duty cycle, safety standards, and crane configuration, you can ensure that your ladle crane will meet both your immediate and future needs. With proper planning and selection, you can ensure your foundry operates smoothly, safely, and efficiently, even in the most demanding environments.
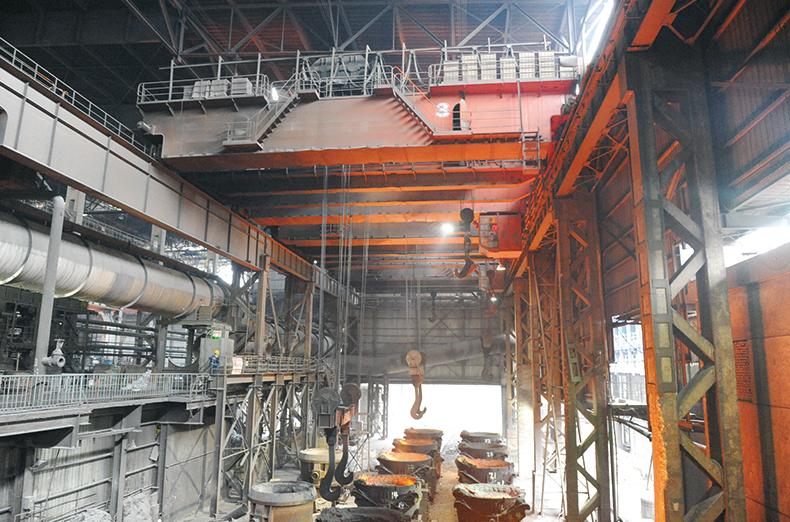
Ladle crane capacity refers to the maximum weight the crane can safely lift and transport. In a foundry, this typically means the total weight of the ladle filled with molten metal, along with any additional rigging or attachments used for secure handling. Ladle crane capacities can range from several tons to over 500 tons, depending on the size and requirements of the foundry.
Key Considerations When Selecting Ladle Crane Capacity
Choosing the correct crane capacity for your foundry depends on various operational factors, including the volume of molten metal handled, safety regulations, and production demands. Here are the main considerations to keep in mind:
1. Weight of the Ladle and Molten Metal
The most critical factor in determining the capacity of a ladle crane is the total weight of the ladle and its molten metal content. You need to calculate the maximum weight the crane will lift during regular operations. This includes:
- The empty weight of the ladle.
- The weight of the molten metal (which can vary depending on the material, such as steel, iron, or aluminum).
- Any additional rigging or accessories used to lift and secure the ladle.
For example, if your foundry uses a ladle that holds 50 tons of molten metal and the ladle itself weighs 10 tons, you’ll need a crane with at least a 60-ton capacity. It is crucial to consider a margin of safety above this capacity to account for fluctuations in load and ensure the crane is not operating at its absolute maximum capacity at all times.
2. Production Scale and Future Growth
Another key consideration is your current and future production scale. It’s important to select a ladle crane that meets not only your present needs but also accommodates potential growth in production capacity. If your foundry is planning to expand or increase production output in the future, opting for a slightly higher crane capacity now may save you from costly upgrades or replacements later on.
For instance, if your foundry is currently handling 50-ton ladles but expects to increase molten metal output in the coming years, it may be prudent to choose a crane with a capacity of 60 or 70 tons. This approach provides flexibility for future growth without compromising efficiency or safety. To learn more about cranes for foundry, click here https://aicraneliftingsolution.com/overhead-cranes/foundry/
3. Work Duty and Operating Conditions
Ladle cranes are exposed to demanding working conditions, including high temperatures, dust, and intensive use. The duty cycle of the crane—how frequently it will be in operation and the intensity of its use—is an important factor when selecting capacity.
Ladle cranes are classified according to duty ratings such as A6, A7, or A8 (based on international standards), with higher ratings suitable for more demanding environments. For example:
- A6: Suitable for medium-duty applications where the crane is used intermittently throughout the day.
- A7: Designed for heavy-duty applications, where the crane is used frequently and must handle high loads.
- A8: Best for very heavy-duty foundries with continuous, intensive usage.
If your foundry operates multiple shifts or has a high production demand, selecting a ladle crane with a higher duty rating and greater capacity will ensure reliable performance over time without frequent downtime or repairs.
4. Safety Requirements and Regulations
Safety is paramount when handling molten metal. Ladle cranes operate in hazardous environments, and overloading them can lead to catastrophic accidents, including the spilling of molten metal or crane failure. To minimize risks, it is important to choose a crane with a capacity that comfortably exceeds your maximum operational load.
In addition, national and international safety standards, such as OSHA (Occupational Safety and Health Administration) or CE (Conformité Européenne) marking for machinery, must be strictly adhered to. Most foundries incorporate at least a 10-15% safety margin into their capacity calculations to prevent overload conditions.
5. Crane Type and Configuration
Ladle cranes come in various types and configurations, including single-girder and double-girder designs, each with different load capacities and operational characteristics. Typically, double-girder cranes offer higher lifting capacities and are more stable for handling heavy loads, making them ideal for larger foundries with high production demands.
Additionally, some ladle cranes are equipped with features such as:
- Rotating mechanisms: Allowing the ladle to be precisely tilted or rotated to pour molten metal.
- Anti-sway technology: Reducing load swinging to enhance safety and precision during metal pouring.
- Remote control systems: Enabling operators to control the crane from a safe distance, minimizing exposure to heat and other hazards.
These additional features should also be factored in when determining the appropriate crane capacity, as they can impact the overall weight the crane must handle.
6. Maintenance and Durability
Durability and ease of maintenance are critical when selecting any crane for a foundry, especially given the challenging operating conditions. Cranes operating in high-heat environments with exposure to molten metal must be built from high-strength, heat-resistant materials. Furthermore, regular maintenance checks should be part of the operational schedule to ensure the crane operates safely at full capacity.
When choosing the right crane capacity, you’ll want to consider the manufacturer's reputation for durability and after-sales support. Investing in a crane that offers easy access to replacement parts, service technicians, and maintenance packages will reduce long-term operational costs and minimize downtime.
Conclusion
Choosing the right ladle crane capacity for your foundry is a decision that directly impacts your production efficiency, safety, and operational success. By considering the total weight of the ladle and molten metal, production scale, duty cycle, safety standards, and crane configuration, you can ensure that your ladle crane will meet both your immediate and future needs. With proper planning and selection, you can ensure your foundry operates smoothly, safely, and efficiently, even in the most demanding environments.
Signatur