3
0
0
Key Features of RMG Cranes for Efficient Container Handling
5
0
In the world of container handling and terminal operations, Rail Mounted Gantry (RMG) cranes play a pivotal role in ensuring efficient movement, storage, and loading of containers. These towering giants, typically used in intermodal terminals, container yards, and port facilities, are designed to operate on rails, enabling high-precision container stacking and efficient handling over long distances.
As global trade continues to expand, the demand for rapid and efficient container handling has pushed innovations in RMG cranes. This article delves into the key features of RMG cranes that make them indispensable for modern container terminals, while highlighting the advantages these features bring in terms of efficiency, safety, and sustainability.
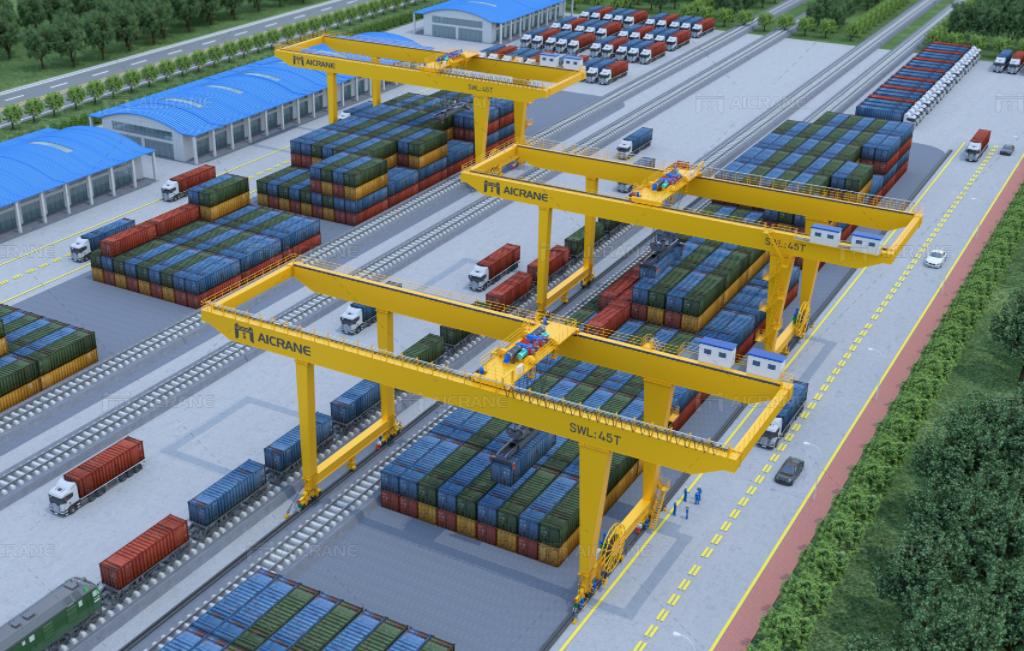
1. High Lifting Capacity and Long Span
One of the most notable features of RMG cranes is their impressive lifting capacity. Typically, these cranes can lift containers ranging from 20 to 65 tons, enabling them to handle even the heaviest ISO-standard containers, including loaded 40-foot and 45-foot units. This high lifting capacity is crucial in fast-paced terminal environments where large container vessels must be unloaded quickly and efficiently.
Additionally, RMG cranes are equipped with long spans that can range between 20 to 40 meters or more, allowing them to cover wide container yards or multiple rail tracks. This capability is essential for maximizing the use of available space in congested areas, as it facilitates optimal container stacking and transport across multiple storage blocks. The combination of high lifting capacity and long span ensures that RMG cranes can handle a high volume of containers with minimal downtime, making them ideal for high-throughput terminals.
2. Precision Control Systems
Precision is critical in container handling, and Aicrane container gantry cranesare equipped with advanced control systems that allow for accurate positioning and placement of containers. These cranes often feature digital control systems with real-time feedback that enable operators to handle containers with millimeter-level precision, reducing the risk of damage during loading or unloading.
Modern RMG cranes may also come with remote control capabilities, allowing operators to control crane movements from a distance, further improving safety and accuracy. The integration of GPS and laser guidance systems enhances container positioning, ensuring that containers are correctly aligned for stacking, rail loading, or transfer to trucks.
3. Automated Operations for Increased Efficiency
Automation is a game-changer in the container handling industry, and RMG cranes are increasingly equipped with automated features that help streamline terminal operations. Automated RMG cranes (ARMGs) are capable of handling containers without human intervention, performing tasks such as stacking, loading, and unloading based on pre-programmed instructions.
These automated systems rely on a combination of advanced sensors, cameras, and software to navigate the terminal and execute precise maneuvers. Automation reduces labor costs, improves safety by minimizing the need for human presence in hazardous areas, and ensures round-the-clock operation. Automated RMG cranes are particularly useful in large terminals where high throughput and efficient space utilization are critical.
4. Anti-Sway Systems for Safe and Smooth Operation
One of the challenges of operating large gantry cranes is controlling sway, which can occur as a result of wind forces or sudden crane movements. RMG cranes are equipped with anti-sway systems that use sensors and control algorithms to minimize sway during container lifting and transport. These systems are crucial for maintaining the stability of the crane and ensuring the safe movement of containers, particularly when handling loads at significant heights.
The anti-sway technology allows operators to handle containers more efficiently, as it reduces the time required to stabilize the load before setting it down or transferring it to a vehicle. This results in faster container handling cycles, leading to higher overall terminal productivity.
5. Energy-Efficient Power Systems
RMG cranes are designed with energy efficiency in mind, which is essential for reducing operational costs and minimizing environmental impact. Modern RMG cranes are equipped with energy-saving technologies, such as regenerative drives, that recover energy during crane operations (e.g., during lowering or braking movements) and feed it back into the system. This reduces the crane’s overall energy consumption and contributes to a more sustainable terminal operation.
Additionally, electric RMG cranes are favored for their low emissions compared to their diesel-powered counterparts, making them a more environmentally friendly option for container terminals looking to reduce their carbon footprint.
6. Integration with Terminal Management Systems
Efficient container handling requires seamless integration between RMG cranes and terminal management systems (TMS). RMG cranes are often connected to these systems, allowing for real-time data exchange that optimizes crane scheduling, container tracking, and yard management. The integration of TMS with RMG cranes ensures that crane movements are synchronized with vessel arrivals, rail schedules, and truck operations, reducing delays and improving overall terminal efficiency.
TMS integration also enables remote monitoring and diagnostics, allowing maintenance teams to track the crane’s performance, predict potential failures, and schedule maintenance during non-peak hours to minimize disruption to terminal operations.
7. Robust Safety Features
Safety is a top priority in any container terminal, and RMG cranes are equipped with a variety of safety features to protect both personnel and equipment. In addition to anti-sway systems, RMG cranes are equipped with collision avoidance sensors that prevent the crane from colliding with other equipment or containers in the yard.
Other safety features include emergency stop systems, overload protection, and wind speed monitoring, which automatically halts crane operations when conditions become too dangerous. By integrating these safety systems, RMG cranes help create a safer working environment for crane operators, ground staff, and other terminal personnel.
8. Customizability for Specific Terminal Needs
Container terminals vary in size, layout, and operational requirements, and RMG cranes are highly customizable to meet these specific needs. Operators can choose from a range of lifting capacities, span lengths, and lifting heights, depending on the volume of containers and the available space in the yard. Additionally, RMG cranes can be equipped with specialized attachments, such as spreaders, to handle containers of different sizes or non-standard loads.
Customization also extends to the level of automation and control options, allowing terminal operators to select the best configuration based on their budget, throughput requirements, and safety needs.
Conclusion
Rail Mounted Gantry (RMG) cranes are vital for the efficient handling of containers in modern terminals. Their high lifting capacity, precise control systems, automated operations, and advanced safety features make them indispensable for ports looking to increase throughput and optimize container storage. As terminals continue to expand and adapt to growing global trade, RMG cranes will play an increasingly important role in driving the efficiency and sustainability of container handling operations. With their energy-efficient designs, customizable options, and integration with terminal management systems, RMG cranes stand at the forefront of innovation in the logistics and shipping industries.
As global trade continues to expand, the demand for rapid and efficient container handling has pushed innovations in RMG cranes. This article delves into the key features of RMG cranes that make them indispensable for modern container terminals, while highlighting the advantages these features bring in terms of efficiency, safety, and sustainability.
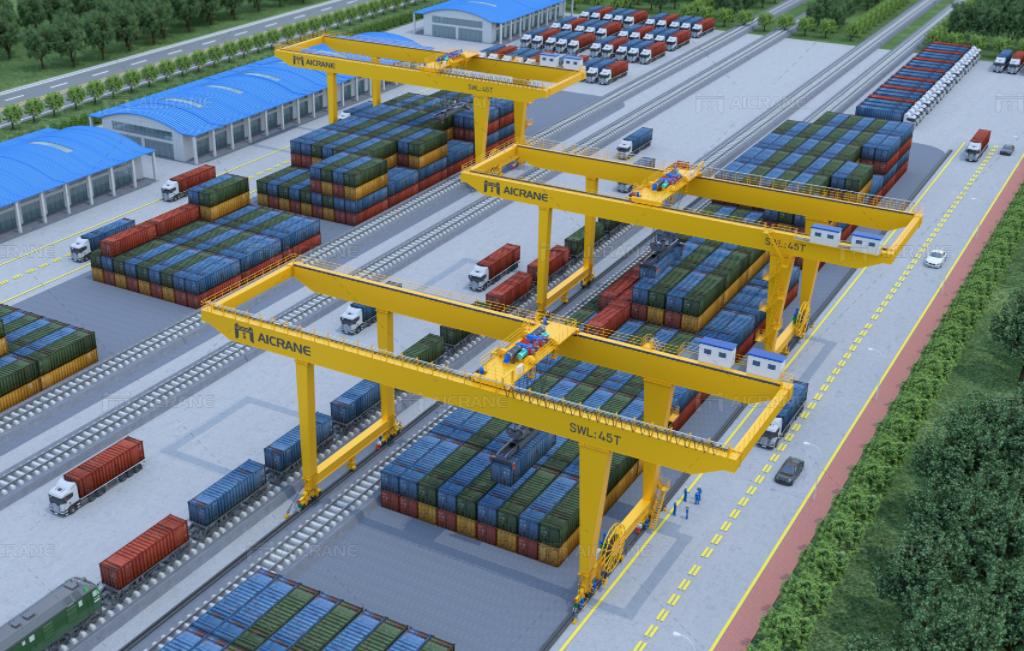
1. High Lifting Capacity and Long Span
One of the most notable features of RMG cranes is their impressive lifting capacity. Typically, these cranes can lift containers ranging from 20 to 65 tons, enabling them to handle even the heaviest ISO-standard containers, including loaded 40-foot and 45-foot units. This high lifting capacity is crucial in fast-paced terminal environments where large container vessels must be unloaded quickly and efficiently.
Additionally, RMG cranes are equipped with long spans that can range between 20 to 40 meters or more, allowing them to cover wide container yards or multiple rail tracks. This capability is essential for maximizing the use of available space in congested areas, as it facilitates optimal container stacking and transport across multiple storage blocks. The combination of high lifting capacity and long span ensures that RMG cranes can handle a high volume of containers with minimal downtime, making them ideal for high-throughput terminals.
2. Precision Control Systems
Precision is critical in container handling, and Aicrane container gantry cranesare equipped with advanced control systems that allow for accurate positioning and placement of containers. These cranes often feature digital control systems with real-time feedback that enable operators to handle containers with millimeter-level precision, reducing the risk of damage during loading or unloading.
Modern RMG cranes may also come with remote control capabilities, allowing operators to control crane movements from a distance, further improving safety and accuracy. The integration of GPS and laser guidance systems enhances container positioning, ensuring that containers are correctly aligned for stacking, rail loading, or transfer to trucks.
3. Automated Operations for Increased Efficiency
Automation is a game-changer in the container handling industry, and RMG cranes are increasingly equipped with automated features that help streamline terminal operations. Automated RMG cranes (ARMGs) are capable of handling containers without human intervention, performing tasks such as stacking, loading, and unloading based on pre-programmed instructions.
These automated systems rely on a combination of advanced sensors, cameras, and software to navigate the terminal and execute precise maneuvers. Automation reduces labor costs, improves safety by minimizing the need for human presence in hazardous areas, and ensures round-the-clock operation. Automated RMG cranes are particularly useful in large terminals where high throughput and efficient space utilization are critical.
4. Anti-Sway Systems for Safe and Smooth Operation
One of the challenges of operating large gantry cranes is controlling sway, which can occur as a result of wind forces or sudden crane movements. RMG cranes are equipped with anti-sway systems that use sensors and control algorithms to minimize sway during container lifting and transport. These systems are crucial for maintaining the stability of the crane and ensuring the safe movement of containers, particularly when handling loads at significant heights.
The anti-sway technology allows operators to handle containers more efficiently, as it reduces the time required to stabilize the load before setting it down or transferring it to a vehicle. This results in faster container handling cycles, leading to higher overall terminal productivity.
5. Energy-Efficient Power Systems
RMG cranes are designed with energy efficiency in mind, which is essential for reducing operational costs and minimizing environmental impact. Modern RMG cranes are equipped with energy-saving technologies, such as regenerative drives, that recover energy during crane operations (e.g., during lowering or braking movements) and feed it back into the system. This reduces the crane’s overall energy consumption and contributes to a more sustainable terminal operation.
Additionally, electric RMG cranes are favored for their low emissions compared to their diesel-powered counterparts, making them a more environmentally friendly option for container terminals looking to reduce their carbon footprint.
6. Integration with Terminal Management Systems
Efficient container handling requires seamless integration between RMG cranes and terminal management systems (TMS). RMG cranes are often connected to these systems, allowing for real-time data exchange that optimizes crane scheduling, container tracking, and yard management. The integration of TMS with RMG cranes ensures that crane movements are synchronized with vessel arrivals, rail schedules, and truck operations, reducing delays and improving overall terminal efficiency.
TMS integration also enables remote monitoring and diagnostics, allowing maintenance teams to track the crane’s performance, predict potential failures, and schedule maintenance during non-peak hours to minimize disruption to terminal operations.
7. Robust Safety Features
Safety is a top priority in any container terminal, and RMG cranes are equipped with a variety of safety features to protect both personnel and equipment. In addition to anti-sway systems, RMG cranes are equipped with collision avoidance sensors that prevent the crane from colliding with other equipment or containers in the yard.
Other safety features include emergency stop systems, overload protection, and wind speed monitoring, which automatically halts crane operations when conditions become too dangerous. By integrating these safety systems, RMG cranes help create a safer working environment for crane operators, ground staff, and other terminal personnel.
8. Customizability for Specific Terminal Needs
Container terminals vary in size, layout, and operational requirements, and RMG cranes are highly customizable to meet these specific needs. Operators can choose from a range of lifting capacities, span lengths, and lifting heights, depending on the volume of containers and the available space in the yard. Additionally, RMG cranes can be equipped with specialized attachments, such as spreaders, to handle containers of different sizes or non-standard loads.
Customization also extends to the level of automation and control options, allowing terminal operators to select the best configuration based on their budget, throughput requirements, and safety needs.
Conclusion
Rail Mounted Gantry (RMG) cranes are vital for the efficient handling of containers in modern terminals. Their high lifting capacity, precise control systems, automated operations, and advanced safety features make them indispensable for ports looking to increase throughput and optimize container storage. As terminals continue to expand and adapt to growing global trade, RMG cranes will play an increasingly important role in driving the efficiency and sustainability of container handling operations. With their energy-efficient designs, customizable options, and integration with terminal management systems, RMG cranes stand at the forefront of innovation in the logistics and shipping industries.
Signatur