3
0
0
Understanding Duty Classes and Their Importance in Heavy Duty Overhead Cranes
9
0
In industrial settings, overhead cranes play a crucial role in material handling, lifting, and moving loads that can range from a few tons to several hundred tons. Heavy-duty overhead cranes are specifically designed for intensive and demanding applications. However, not all heavy-duty overhead cranes are created equal, and selecting the right crane for your application requires an understanding of duty classes. Duty classes, established by organizations such as the Crane Manufacturers Association of America (CMAA), provide guidelines for the crane's durability and expected performance based on load frequency, load weight, and operating environment. By understanding these classes, companies can better ensure efficiency, longevity, and safety in their material handling processes.
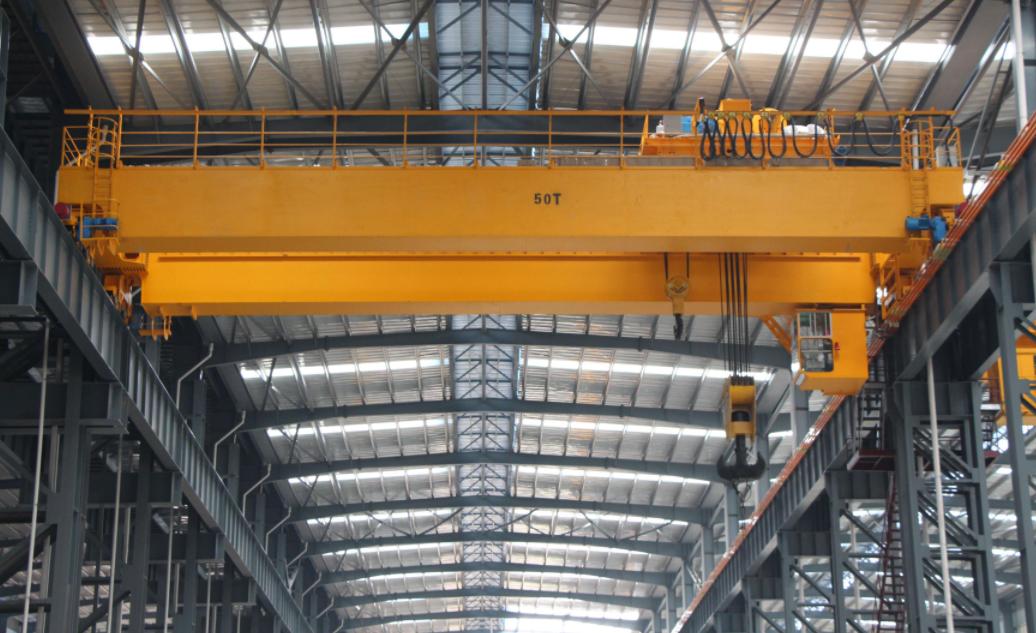
What Are Duty Classes in Overhead Cranes?
Duty classes, also known as service classifications, categorize cranes based on how often and intensely they are used. The most widely recognized duty classes are those defined by the CMAA, which range from Class A (Standby or Infrequent Service) to Class F (Continuous Severe Service). These classifications help specify a crane's suitability for particular types of work environments and loading conditions. Each class reflects the crane’s expected service life, number of cycles, and weight of loads it can handle regularly.
The duty class of a crane is determined by factors such as:
Overview of CMAA Duty Classes
[ol]
Class A - Standby or Infrequent Service
Class B - Light Service
Class C - Moderate Service
Class D - Heavy Service
Class E - Severe Service
Class F - Continuous Severe Service
[/ol]
Importance of Choosing the Correct Duty Class
Selecting a crane with the appropriate duty class for your operation has significant advantages in terms of productivity, longevity, and safety.
1. Optimized Performance
2. Enhanced Safety
3. Extended Lifespan
4. Cost Efficiency
Factors to Consider When Determining the Right Duty Class
Frequency of Operation
Average and Maximum Load Weight
Operating Environment
Work Cycle Duration
Conclusion
Understanding duty classes and selecting the right classification is essential for efficient, safe, and cost-effective crane operation. A crane that matches the operational demands not only enhances productivity but also minimizes the risk of accidents, prolongs equipment life, and reduces maintenance expenses. Whether for a light-duty assembly line or a heavy-duty steel mill, carefully matching a crane's duty class to the specific application ensures optimized performance and safety.
By analyzing your operational needs and consulting with crane experts, you can make informed decisions about duty classes. Choosing a crane that aligns with the right duty class ensures that your equipment is an asset that supports your industrial activities for years, providing robust service without unnecessary costs or risks.
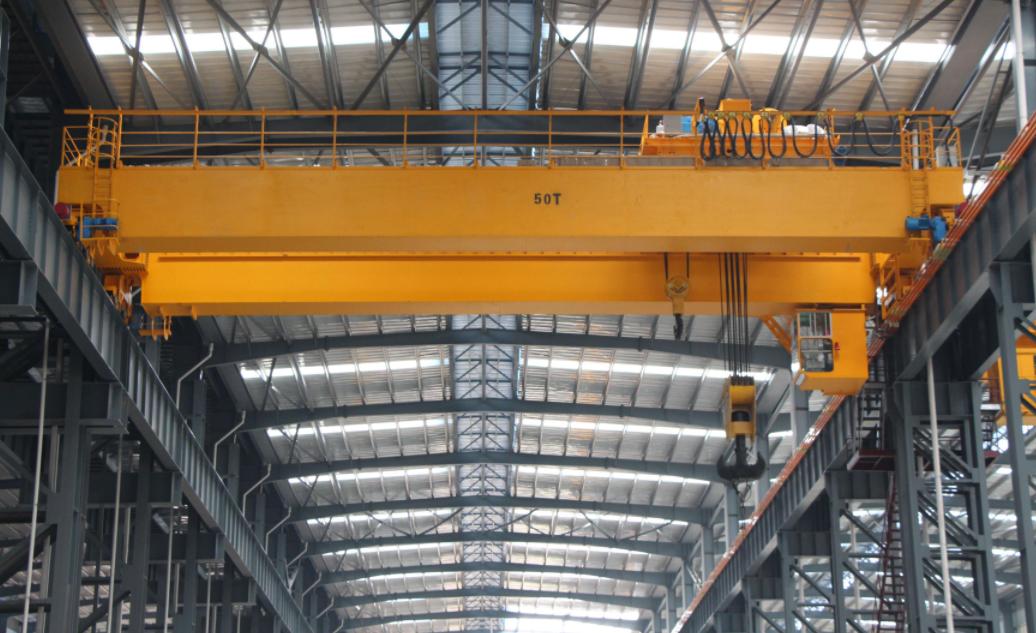
What Are Duty Classes in Overhead Cranes?
Duty classes, also known as service classifications, categorize cranes based on how often and intensely they are used. The most widely recognized duty classes are those defined by the CMAA, which range from Class A (Standby or Infrequent Service) to Class F (Continuous Severe Service). These classifications help specify a crane's suitability for particular types of work environments and loading conditions. Each class reflects the crane’s expected service life, number of cycles, and weight of loads it can handle regularly.
The duty class of a crane is determined by factors such as:
- Frequency of use: How often the crane will be used per day.
- Load weight: The average and maximum loads the crane will lift.
- Operating environment: Conditions like temperature, humidity, and corrosive substances can impact the crane's performance.
- Work cycles: Number of lifting and lowering cycles performed over a period.
Overview of CMAA Duty Classes
[ol]
- Characteristics: Light service, minimal frequency of use.
- Typical Applications: Utility buildings, maintenance shops.
- Example Uses: Cranes in this class are ideal for environments where lifting is needed only occasionally, such as in a maintenance shop where large items are lifted only when repairs are necessary.
- Characteristics: Light duty, with lifting performed a few times per hour and relatively low load weights.
- Typical Applications: Light assembly and maintenance work.
- Example Uses: Cranes in light duty class are applied in assembly workstations where lightweight components need occasional moving.
- Characteristics: Moderate frequency of use, handling heavier loads than Class B.
- Typical Applications: General machine shops and warehouses.
- Example Uses: Cranes in this category are suitable for workspaces where lifting and moving happen a few times per hour and loads are moderate in weight.
- Characteristics: Frequent, heavy-duty lifting with greater load weights and higher frequency.
- Typical Applications: Foundries, heavy machining, and fabricating industries.
- Example Uses: This class is suitable for production-oriented facilities where loads may be heavy and lifted regularly.
- Characteristics: Very high-frequency operation with nearly full capacity loads.
- Typical Applications: Steel mills, large manufacturing plants.
- Example Uses: Class E cranes are ideal for demanding environments where heavy loads are lifted and moved constantly, such as in steel production or large industrial facilities.
- Characteristics: Extremely demanding service, often operating 24/7 with near full-capacity loads.
- Typical Applications: Foundries, steel mills, and other environments requiring continuous, heavy-duty service.
- Example Uses: Used in extremely rigorous settings, cranes in this class support round-the-clock operations in manufacturing environments with high-stress conditions.
[/ol]
Importance of Choosing the Correct Duty Class
Selecting a crane with the appropriate duty class for your operation has significant advantages in terms of productivity, longevity, and safety.
1. Optimized Performance
- Cranes designed for higher duty classes, like Class E or F, are engineered to handle rigorous and continuous use. This ensures that they can perform at their peak even under demanding conditions, such as in steel mills or foundries. Choosing the correct duty class enhances the crane’s overall performance, allowing it to handle work cycles and load demands effectively.
2. Enhanced Safety
- Using a crane beyond its designed duty class poses significant safety risks. For example, a Class C crane used in a Class E environment might fail due to overuse or excessive weight, leading to potential accidents. Ensuring that the crane’s duty class matches the workload helps minimize wear and tear, preventing unexpected failures and maintaining a safe working environment.
3. Extended Lifespan
- Each duty class specification is designed to ensure that the crane operates efficiently for its intended use without premature wear. When a crane operates within its designated duty class, its components, such as motors, brakes, and controls, are less likely to experience stress-related failures. This longevity reduces the need for frequent repairs or replacements, helping to lower long-term maintenance costs.
4. Cost Efficiency
- While cranes designed for higher duty classes may have higher initial costs, they often result in long-term savings by avoiding excessive maintenance and downtime. Selecting a crane with an appropriate duty class ensures cost efficiency, as the crane will not need costly repairs due to overuse or unplanned upgrades to meet operational demands.
Factors to Consider When Determining the Right Duty Class
Frequency of Operation
- The more frequently a crane is used, the higher the duty class it should be. For example, if a crane is needed multiple times per hour, a Class D or higher crane would be appropriate.
Average and Maximum Load Weight
- Consider both the average and maximum load weight the crane will need to lift. If the maximum load is near the crane's rated capacity, a higher-duty-class crane will provide the necessary support for safe operations.
Operating Environment
- Some environments, like foundries or steel mills, expose cranes to extreme heat, dust, and even corrosive elements. In such cases, selecting a duty class suited for severe conditions, like Class E or F, is essential to ensure the crane withstands the operating conditions without excessive wear.
Work Cycle Duration
- The length and frequency of the crane’s lifting and movement cycles contribute to wear on its components. Facilities requiring continuous operation should consider higher duty classes to ensure the crane can handle the workload sustainably.
Conclusion
Understanding duty classes and selecting the right classification is essential for efficient, safe, and cost-effective crane operation. A crane that matches the operational demands not only enhances productivity but also minimizes the risk of accidents, prolongs equipment life, and reduces maintenance expenses. Whether for a light-duty assembly line or a heavy-duty steel mill, carefully matching a crane's duty class to the specific application ensures optimized performance and safety.
By analyzing your operational needs and consulting with crane experts, you can make informed decisions about duty classes. Choosing a crane that aligns with the right duty class ensures that your equipment is an asset that supports your industrial activities for years, providing robust service without unnecessary costs or risks.
Signatur