12
0
0
What is Silicon Carbide Bricks?
Silicon carbide bricks are specialized refractory materials designed to withstand extreme temperatures, abrasive environments, and corrosive conditions. Known for their remarkable durability and high performance, these bricks are a critical component in various industrial applications, including metallurgy, ceramics, glass production, and more. This article delves into the composition, properties, manufacturing processes, and applications of silicon carbide bricks, offering a comprehensive overview of their significance in industrial operations.
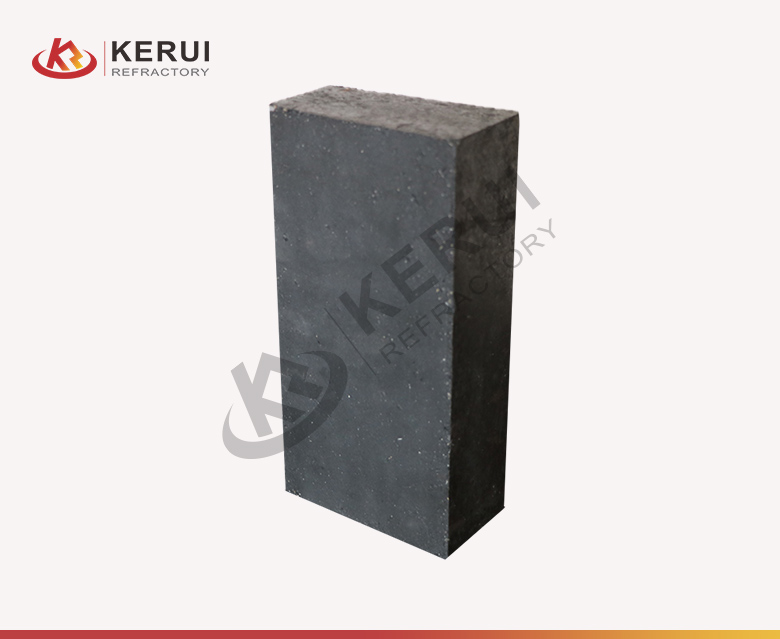
Composition and Properties
1. Composition
Silicon carbide bricks are primarily composed of silicon carbide (SiC), a compound formed by the combination of silicon and carbon. Silicon carbide is a ceramic material known for its exceptional hardness and thermal stability. The raw materials used to produce silicon carbide bricks typically include silica sand, petroleum coke, and other carbon sources. During the manufacturing process, these materials are subjected to high temperatures in an electric furnace, where they react to form silicon carbide.
2. Properties
Silicon carbide bricks possess a range of properties that make them suitable for demanding applications:
Manufacturing Process
The manufacturing of silicon carbide bricks involves several key steps:
1. Raw Material Preparation
The primary raw materials for silicon carbide bricks include silica sand, petroleum coke, and other carbon sources. These materials are finely ground and mixed to achieve the desired chemical composition.
2. Mixing and Molding
The prepared raw materials are mixed with a binder to form a paste. This paste is then molded into the desired shape of the bricks. The molding process can involve various techniques, including pressing, extrusion, or casting, depending on the intended application and the required brick dimensions.
3. Sintering
After molding, the bricks undergo a sintering process in an electric furnace. During sintering, the bricks are heated to high temperatures, typically between 1,500°C and 2,500°C (2,732°F and 4,532°F), to promote the formation of silicon carbide from the raw materials. The high temperature causes the particles to bond together, resulting in a dense and durable ceramic material.
4. Finishing
Once sintering is complete, the bricks are cooled and subjected to finishing processes, such as grinding or polishing, to achieve the desired surface finish and dimensional accuracy. The finished bricks are then inspected for quality and consistency before being packaged and shipped for use.
Applications
Silicon carbide bricks are used in a wide range of industrial applications due to their unique properties. Some of the most notable applications include:
1. Metallurgical Industry
In the metallurgical industry, silicon carbide bricks are employed in several high-temperature and abrasive environments:
2. Ceramic Industry
The ceramic industry benefits from the use of silicon carbide bricks in high-temperature kilns and other equipment:
3. Glass Industry
In the glass industry, silicon carbide bricks are used for their ability to withstand extreme temperatures and corrosive environments:
4. Chemical Industry
The chemical industry relies on silicon carbide bricks for their chemical resistance and thermal stability:
5. Petrochemical Industry
In the petrochemical industry, silicon carbide bricks are used in:
6. Power Generation
Silicon carbide bricks are also used in power generation:
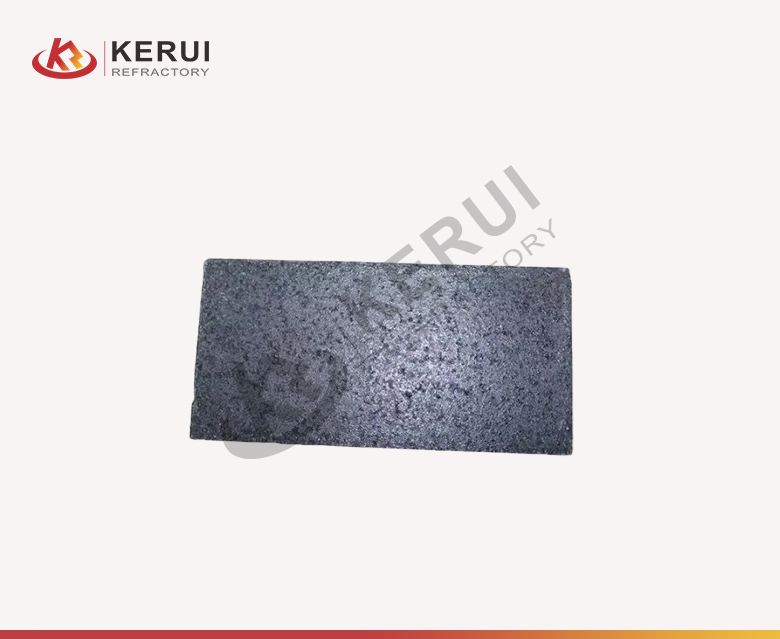
Advantages and Challenges
1. Advantages
Silicon carbide bricks offer several advantages:
2. Challenges
Despite their benefits, silicon carbide bricks also face some challenges:
Conclusion
Silicon carbide bricks are an indispensable component in many industrial applications, providing exceptional performance in high-temperature and corrosive environments. Their composition, properties, and manufacturing process contribute to their effectiveness and durability. From metallurgy and ceramics to glass production and power generation, silicon carbide bricks play a vital role in maintaining efficiency and reliability across various sectors.
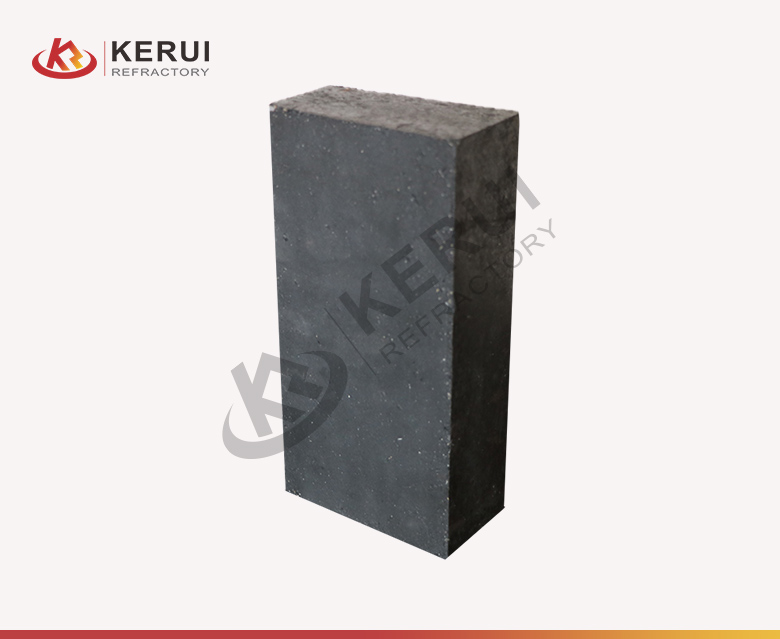
Composition and Properties
1. Composition
Silicon carbide bricks are primarily composed of silicon carbide (SiC), a compound formed by the combination of silicon and carbon. Silicon carbide is a ceramic material known for its exceptional hardness and thermal stability. The raw materials used to produce silicon carbide bricks typically include silica sand, petroleum coke, and other carbon sources. During the manufacturing process, these materials are subjected to high temperatures in an electric furnace, where they react to form silicon carbide.
2. Properties
Silicon carbide bricks possess a range of properties that make them suitable for demanding applications:
- High Hardness: Silicon carbide is one of the hardest known materials, making the bricks highly resistant to abrasion and wear. This property is crucial in environments where mechanical wear is prevalent.
- Thermal Conductivity: Silicon carbide bricks have excellent thermal conductivity, which ensures efficient heat transfer and uniform temperature distribution in high-temperature applications.
- Thermal Shock Resistance: The ability to withstand rapid temperature changes without cracking is a key characteristic of silicon carbide bricks. This thermal shock resistance is essential for applications involving fluctuating temperatures.
- Chemical Resistance: Silicon carbide bricks exhibit high resistance to chemical corrosion, including acids, alkalis, and molten metals. This makes them suitable for environments with aggressive chemical substances.
- High Melting Point: Silicon carbide has a melting point of approximately 2,700°C (4,892°F), allowing silicon carbide bricks to endure extreme temperatures without degrading.
Manufacturing Process
The manufacturing of silicon carbide bricks involves several key steps:
1. Raw Material Preparation
The primary raw materials for silicon carbide bricks include silica sand, petroleum coke, and other carbon sources. These materials are finely ground and mixed to achieve the desired chemical composition.
2. Mixing and Molding
The prepared raw materials are mixed with a binder to form a paste. This paste is then molded into the desired shape of the bricks. The molding process can involve various techniques, including pressing, extrusion, or casting, depending on the intended application and the required brick dimensions.
3. Sintering
After molding, the bricks undergo a sintering process in an electric furnace. During sintering, the bricks are heated to high temperatures, typically between 1,500°C and 2,500°C (2,732°F and 4,532°F), to promote the formation of silicon carbide from the raw materials. The high temperature causes the particles to bond together, resulting in a dense and durable ceramic material.
4. Finishing
Once sintering is complete, the bricks are cooled and subjected to finishing processes, such as grinding or polishing, to achieve the desired surface finish and dimensional accuracy. The finished bricks are then inspected for quality and consistency before being packaged and shipped for use.
Applications
Silicon carbide bricks are used in a wide range of industrial applications due to their unique properties. Some of the most notable applications include:
1. Metallurgical Industry
In the metallurgical industry, silicon carbide bricks are employed in several high-temperature and abrasive environments:
- Electric Arc Furnaces (EAFs): Silicon carbide bricks are used to line electric arc furnaces, which are utilized for melting and refining metals such as steel and iron. The bricks protect the furnace lining from intense heat and corrosive molten metal.
- Blast Furnaces: Silicon carbide bricks are used in blast furnaces for iron production. Their resistance to high temperatures and abrasive conditions ensures the longevity of the furnace lining.
- Ladle Linings: Silicon carbide bricks are used to line ladles, which are used to transport and handle molten metal. The bricks provide resistance to the molten metal and slag, enhancing the ladle's durability and efficiency.
2. Ceramic Industry
The ceramic industry benefits from the use of silicon carbide bricks in high-temperature kilns and other equipment:
- Kiln Linings: Silicon carbide bricks are used to line kilns where ceramics and other materials are fired. Their high thermal conductivity ensures even heat distribution, while their thermal shock resistance prevents cracking.
- Burners and Combustion Chambers: Silicon carbide bricks are used in the construction of burners and combustion chambers that operate under high temperatures. Their durability and resistance to chemical attack make them ideal for these applications.
3. Glass Industry
In the glass industry, silicon carbide bricks are used for their ability to withstand extreme temperatures and corrosive environments:
- Glass Melting Furnaces: Silicon carbide bricks are employed to line furnaces used for melting raw materials into glass. Their high melting point and thermal shock resistance are crucial for maintaining furnace performance.
- Batch Furnaces: Similar to glass melting furnaces, batch furnaces require bricks that can endure high temperatures and corrosive conditions. Silicon carbide bricks provide the necessary protection and efficiency.
4. Chemical Industry
The chemical industry relies on silicon carbide bricks for their chemical resistance and thermal stability:
- Chemical Reactors: Silicon carbide bricks are used to line reactors that handle aggressive chemicals and operate at high temperatures. Their resistance to chemical corrosion ensures the longevity of the reactor lining.
- Acid-Resistant Linings: Silicon carbide bricks are employed in applications requiring resistance to acids and other corrosive substances. They provide effective protection in environments with harsh chemical conditions.
5. Petrochemical Industry
In the petrochemical industry, silicon carbide bricks are used in:
- Reforming Furnaces: These furnaces are used to convert hydrocarbons into valuable chemicals. Silicon carbide bricks are used to line reforming furnaces, where they withstand high temperatures and corrosive gases.
- Cracking Furnaces: Silicon carbide bricks are used in cracking furnaces to handle the extreme conditions involved in breaking down hydrocarbons. Their durability and resistance to thermal and chemical stresses are essential for efficient operation.
6. Power Generation
Silicon carbide bricks are also used in power generation:
- Coal Gasification Plants: These plants convert coal into gas for use in power generation. Silicon carbide bricks are employed in gasifiers due to their ability to withstand high temperatures and corrosive gases.
- Waste Incinerators: Silicon carbide bricks are used in waste incinerators to manage the extreme conditions and corrosive substances produced during waste combustion.
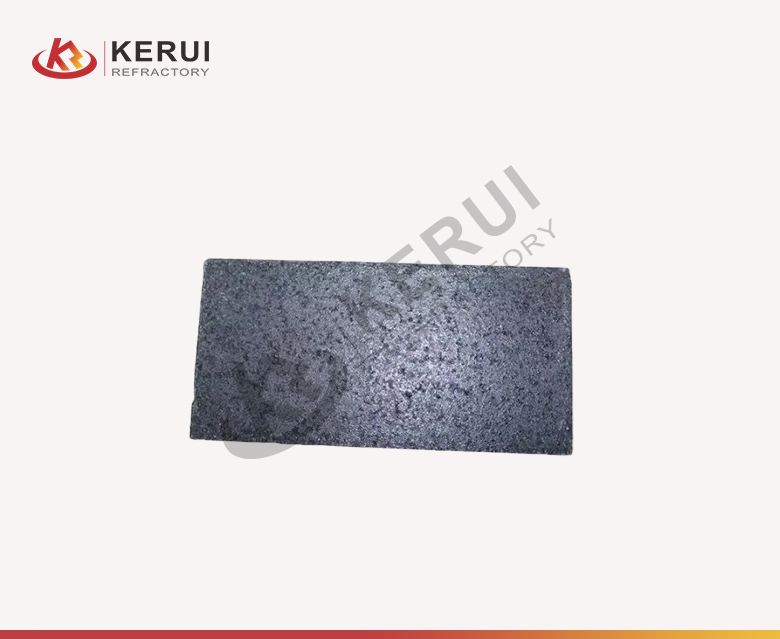
Advantages and Challenges
1. Advantages
Silicon carbide bricks offer several advantages:
- High Performance: Their hardness, thermal conductivity, and resistance to thermal shock and chemical attack ensure reliable performance in demanding applications.
- Durability: Silicon carbide bricks have a long service life due to their resistance to abrasion and wear. This reduces maintenance costs and downtime.
- Efficiency: Their ability to maintain consistent temperatures and resist thermal shock improves the efficiency of industrial processes.
2. Challenges
Despite their benefits, silicon carbide bricks also face some challenges:
- Cost: The high cost of raw materials and manufacturing can make silicon carbide bricks expensive. This can be a consideration for industries with budget constraints.
- Handling and Installation: The brittle nature of silicon carbide requires careful handling and installation to prevent damage. Proper techniques are necessary to ensure the bricks perform effectively.
- Wear and Tear: Over time, silicon carbide bricks can experience wear and tear, especially in highly abrasive environments. Regular inspection and maintenance are required to address any issues.
Conclusion
Silicon carbide bricks are an indispensable component in many industrial applications, providing exceptional performance in high-temperature and corrosive environments. Their composition, properties, and manufacturing process contribute to their effectiveness and durability. From metallurgy and ceramics to glass production and power generation, silicon carbide bricks play a vital role in maintaining efficiency and reliability across various sectors.